Glue Applicator Choices
Cabinetmakers discuss efficient, non-messy ways to apply glue to solid wood staves when making up door panel blanks. July 10, 2009
Question
I have a question about the glue spreader below. It is used for distributing glue on staves that will be laminated together for raised panels etc. The concept seems pretty simple. A perforated metal pan lives in a pond of glue. As you step on the lever at the bottom this pan raises to present a pattern of glue that you press the long edge of a stick onto.
How viable is this approach for a small shop? Does the glue have such a short pot life that clean up for the machine would wipe out any labor gains from the machine?
Also: are there any better ways to distribute glue on a long stave? We get way more squeeze out than I want and it is always a painful experience to either wipe it off when wet or scrape it when dry. Does anybody have a better solution for getting the right amount of glue along the edge of a laminated board?
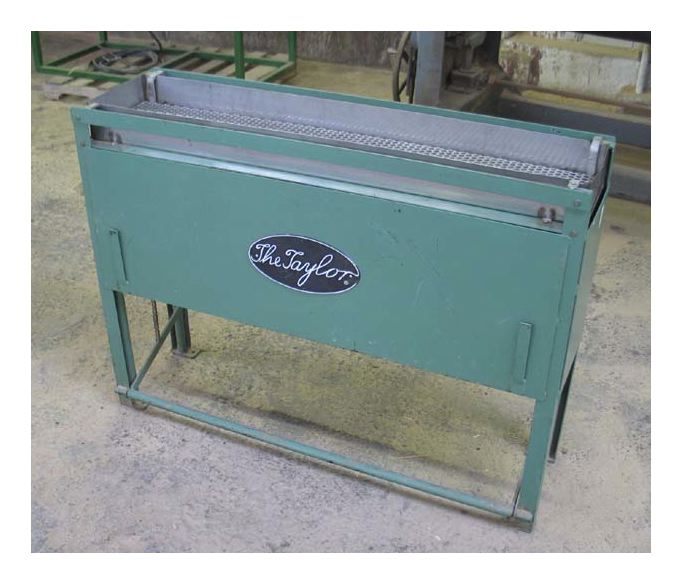
Click here for higher quality, full size image
Forum Responses
(Cabinetmaking Forum)
From contributor T:
We use a pressurized glue tank. It’s a Scheenburge and has 15 years worth of glue on it. I can't read the label. We have two lines coming off it, one for 8M dowels and another for biscuits. Nozzles twist on/off. When not in use the nozzles sit attached to squeeze trigger in a coffee can filled with water. All this is on a little rolling cart set up for this. There are many different nozzles available.
From contributor D:
We considered one of these long ago, but ended up with a glue roller from Virutex. The Virutex has a top wheel the partially rests in the glue. You roll your piece across it.
From the original questioner:
The problem I am trying to solve is one of uneven distribution and/or too much glue. We usually only coat one edge of the lamination and leave the other one dry. The extra glue squeeze out is what I am trying to manage. This is a messy thing to clean up when glue is wet and takes a lot of muscle when the glue is so hard it needs to be scraped. We sometimes try to time the glue-ups such that the glue can harden enough to scrape but not be so hard it takes Hercules to get the job done. We flatten these panels on the jointer after glue up and it would be nice to not have so much excess glue passing over the jointer knives. It would be great to find some kind of applicator. I'm thinking that the pressurized pot contributor T mentions would be worth looking at. I'm guessing you could engineer a fence on the glue applicator to keep the glue bead centered where you want it and maybe some kind of spreading mechanism that follows the glue bead?
From contributor D:
Your fence idea would work with this item. The top roller is textured rubber, which better controls the glue application. It's small, easy to clean and cheap enough that that you could try it and see.
From the original questioner:
That looks interesting. Did you not say you tried and abandoned this method? If so, what is the roller made of? Is it hard to clean?
From contributor D:
We did try this method and eventually abandoned it. However, we do so little edge gluing that I don't think my experience is a good barometer. Knowing what I know, I think your vertical fence idea is a good one. Basically, the rubber roller just lifts off. You rinse it in the sink and dump it in a bucket of water until next use. The glue pot simply gets the lid put on. Supposedly you can mist some water on top of the glue and will keep longer. The roller is hard rubber with a diamond texture imbedded into it. From what I recall, it applied the perfect amount of glue with only pinhead size beads squeezing out.
From contributor A:
JLT makes a smaller version of your glue applicator. It works about the same but is not as long and holds less glue so it stays fresher longer. Our’s used to get a dry crust between jobs on top of the glue. We switched to Titebond brand and that problem went away. We do about three kitchens a month and the glue stays fresh.
Squeeze-out does occur but that is better than a starved joint. We never scrape or joint panels after glue up. Unnecessary non-value added steps. I thought scraping was needed until I talked to another cabinet maker who did not scrape. I tried it and never looked back. I’ve never had a problem plugging widebelts or planer blades. Our panels are flat and true coming out of the sander. Run them at an angle so the glue lines don't have a chance to build up on the belts.
We glue up panels with the good side up in the clamp. Run though the sander (planer/sander now) good side down on the first pass. The glue levels out more on the good side of the panel as it dries in the clamp. It is flatter and truer than the dried drips on the bottom side so is true enough to run on the feed belt of the sander.