Maintenance and Care for a Timberking 1220
Timberking bandmill owners share tips on maintenance, care and use. March 26, 2009
Question
I just purchased a 1220 Timberking and am wondering if any others have this machine. I wish I had done more research before buying as I am not very impressed thus far. Nothing was set up when machine arrived, although according to the manual, it was supposed to be from the factory. Anyway, I figured that out, and then the guide bearing seized up. TK sent me 6, so I guess that’s common. I have cut less than 2k and now the belt keeps jumping off. TK's sending a new belt, but says that happens sometimes with new saws. Maybe my expectations were too high, but any info on this machine’s quirks would be appreciated.
Forum Responses
(Sawing and Drying Forum)
From the original questioner:
I have to say the mill cuts really good when it works. If I can get the bugs out of it, I think I'll be satisfied with it. Some engineering things I personally would have done differently, but it seems heavy built. Oh well, that's what torches and welders are for, right?
From contributor S:
I've owned a TK1220 for a while. I'll agree it didn't come ready to saw and the manual could use some improvement. Being as there was still quite a bit of snow on the ground when mine was delivered, I had time to study the manual thoroughly. I checked all the alignments before attempting to saw. My first boards were perfect and I was hooked! My mill is set up on a concrete slab and under a roof. I have it blocked with timbers fastened to the slab, no movement when loading big logs. I'll give the guides a shot of WD-40 occasionally and oil the trolly wheels. Being under roof is a big advantage to maintaining. I researched portable sawmills for 12 years before deciding to buy one. I have no regrets for choosing the TK1220. Anytime I've called or emailed with a question or needed a part I've got a quick response.
From the original questioner:
That makes me feel better. You have the ideal situation for this mill. I installed my own highway kit as portability was required. The timber I cut is free and I don't like logging with a trailer and pickup. I try to keep mine under cover when not in use and keep it clean. TK has helped when called, I just get aggravated to have to work on something brand new, I've already got enough junk to keep me busy.
From contributor V:
I've just completed the second season of cutting with my 1220 and must say I've cut thousands of feet of poplar, pine, cherry, and less quantities of maple, locust, walnut, hickory. My mill hasn't been under a roof since I pulled it home from the factory to PA. My mill cut great from the get go, and a few months ago I realigned all the wheels, and guides. I always spray the guide bearings down with WD-40 when done cutting. I have received one new set of bearings in two years. The log on the mill is a 28 inch diameter. hickory 10 feet long. The stacks of lumber in the background are representative of what I cut in about three weekends without helpers. The only thing I would change if ordering again would be to upgrade to the 20 horse engine. If you follow the manual closely, and set your mill to their specs you should be able to slice one sixteenth inch thick veneer off your logs.
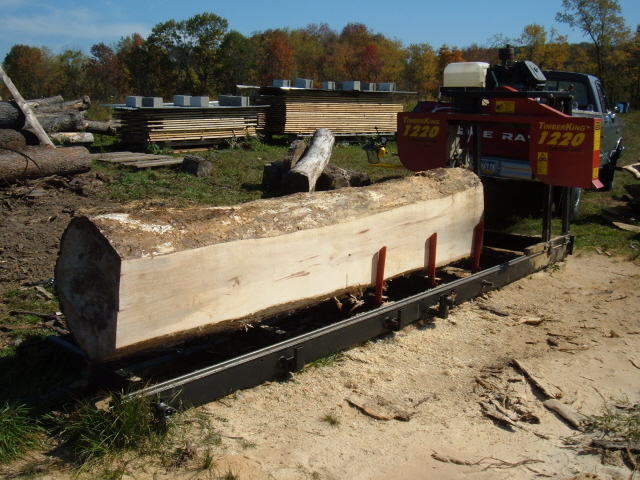
Click here for higher quality, full size image
From the original questioner:
Thanks for the vote of confidence. I tightened the motor/belt and cut about 200bf of dry ERC without any problems. Guess most of my problem is the learning curve. Yet to put any hardwood on it yet, but will be cutting some 25" plus green gum for cattle gap. Your setup does look like a champ.
From contributor C:
I've had a 1220 for about a year now and I’m pretty happy with it but it seems that I have a bearing or to start to stick just about every log I cut. I spray them with WD-40 but the one set that continually gets blasted with sawdust and water constantly stick up. Sometimes I just saw with a bearing or two stuck because I am sick of replacing them. Does anyone have any suggestions?
From the original questioner:
Since looking into this I've found many TK owners have recommended drilling a tiny hole the bearing seal, and using a grease gun needle, shooting a pump or two after cutting. Some claim years of trouble free use. It certainly wouldn’t hurt to try. I’m still having a problem with belt twisting or coming off when engaging clutch. I'm not above putting an idler wheel on the sucker.
From contributor M:
I’ve heard of putting a hole in side of bearing shield. I measured the hole in one of my chainsaw bars and it was .070 inches. I carefully drilled a .070 hole in the old bearing shield on my mill and I had to replace the other one because it was rough. I purchased the small grease gun that is sold in the chainsaw section al Lowe's. The old bearing has 575 hours on it and runs as good as new. I put one squirt in the bearing about every 20 hours.
Too much grease will cause a bearing to overheat and fail. I also purchased the bearings on my TK B20 from a store on Ebay for $9.95 each and TK charges $44.00. It is the same class and quality as the ones sold by TK. I also purchased the ideler wheel bearings on there also for much less. Be sure you purchase bearings that are sealed and shielded on both sides.
From contributor R:
If you are using sealed bearings you can pop the seal out and grease or oil the bearing. Use an ice pick or something similar to remove the seal.
From contributor N:
I've run my bearings thousands of hours now with the little hole and greasing them, I know you can pop the seal out but the hole and needle nose grease gun is easy and gets done on a regular basis. If the 1220 is running the same guide bearing setup as the 1600 I'd really think about a Cooks retrofit with greasable bearings. I just thing the bearings in the 1600 are too small and it has too many.
From contributor M:
If you pop the shield and seal out of the bearing then coolant, sawdust, etc. will enter the bearing and it would only last an hour or two. The coolant will flush the grease out of the bearing. Bearings are designed not to exceed a certain RPM and load. As with my TK B20 I have been making modifications to my mill for two years to compensate for TK's poor assembly and not making the proper improvements on their mills. If I had not had a background in machinery I would have returned it on their 30 day warranty. After five hours of run time I stopped the mill and almost disassembled the mill and went completely through it.
They have a good design but when I was at their facility the sales people had the mindset and bragged about "we are selling them faster than we can produce them" so they in my opinion are throwing them together. I feel sorry for the guys in the service department because if management would fix the problem the service guys job would be so much better and TK would save a ton of money.
From contributor U:
I own a timberking 1220 which I purchased about five years ago. I have been through a lot with it as I run it seven days a week, sawing mostly black locust. Again, if you research back you will find boat loads of information on it, the break downs I had on it, and how I beefed it up in repair.
The biggest things you need to know are that the mill comes adjusted (supposedly), but nothing is tight, and will fall out of whack at least twice before all the set screws dig in a bit and grab the metal they contact, especially on the wheel spindle adjustments.
You need a solid foundation and bolt the mill down. I load my mill with a large knuckleboom, and bent the mill once. That was a horrifying experience because you cannot simply weld on to the mill frame - it will warp badly! If you look on the top of the frame where the round rail track is and find where it is welded, you will see directly under every weld is a reverse weld on the bottom of the frame. This is a large circular spot weld that reverses the tension on the top weld.
I have upgraded the leveling legs from 3/4" to 1-1/2" diameter threaded rod, with a large flat base with plenty of room to drill and bolt the mill down to its six 8x8 blocks, which are rebarred 4' in to the ground about 10 times each, staggered in different directions. If you oil your guide bearings after every use they will last much longer. Use any oil, but not WD-40 or other sprays! Run Timberwolf blades at 13' 9", .045 thick, 3/4 pitch and you will be highly impressed, enough to throw your timber king blades away.
My best tip: oil the roller bearings underneath the mill carriage (the ones that ride the track), and the brass bushings on the cable drive pulleys, then adjust the cable tension. You should always be able to give the mill a good push with the drive handle disengaged, and see it travel about four or five feet.
Cables need frequent adjustment every couple cuts when they are new so they stretch. I run my mill fast and sometimes when it is cold the cable will slightly warms up to a point you can’t feel, and it expands it slightly, making it loose tension. Replace the cable if it starts to fray, because the tension becomes a major problem. I do have one extension on my mill so the longer cable may be more of an issue for me vs. a shorter mill. Hope you got the 20 hp koehler!
It is still in my mind the best mill for the buck its size class, but the company has horrible customer service, and a horrible manual. They do not allow the customer to understand what they are getting into, because they think it will drive them away to another company, but the truth is every mill has it's quirks that the maker won’t mention because they are salesmen. This is the first mill I have owned, but the 6th mill I have run.
I also want to add, that I have bent the heck out of the dogs many times, and had to beef them up. There is no reason for them to line up with the little square stops on the mill deck for cants, so I welded a 1-1/2" plate the same height as the log stop 90 degrees to the stop, welded on both sides. If you make any more log clamp sets, make sure you use the same grade of thick pipe they use at the factory, because thinner pipe will turn oval, and out of square very quickly.
From contributor E:
Over here I'm running a B20 with 7000 hours on it and it's held up great, once I got the setworks fixed I haven't had to get anything from TK for over three years and I don't get any sale flyers anymore. I kind of wish they’d send something out twice a year.
From contributor I:
I have a 1220 for about four to five years . I am a weekend type of cutter. I brought it home with the extension and quickly leveled and set it up. I have cut every type of hard wood and soft wood. I have never changed any of the factory set ups of the blades/wheels. I do go through a lot of guide bearings and buy them by the bag full. I have added a DC motor to the travel hand wheel and a homemade festoon. It took me several changes in belt pulleys to get a good ratio for both forward and reverse. I had to add a jack shaft between the motor and the hand crank wheel. At 66 years old and my arthritis this really helps a lot. I think the overall mill is very lightly built, but in all honesty I have had no issues as of yet. I would guess I have sawed 8000 feet.
From contributor W:
If you have Cook’s guides then I think they have grease fittings on them. Most bearings have a manufactures number etched on the outer race of the bearing such as the bearing for my B20 is 5304-2RS which means it is a 5304 bearing and is shielded and sealed on both sides.
The comments below were added after this Forum discussion was archived as a Knowledge Base article (add your comment).
Comment from contributor B:
I have owned a 1220 for almost four years now and I run it like a dog. I do understand your frustration on certain issues of this unit. One tip I can give you of a few is regarding the guide bearings. Turn out six brass bushings to fit the bolts on the "ID" and then fit the "OD for a 6202 bearing. In Florida I cannot find the OEM size for fewer than $15 each. My mill is on a slab, under roof, and elevated approximately 24 inches to help with moving the work closer the operator. It also makes it easier to clean out under the mill.