Power Comparison Between Electric and Gasoline-Powered Bandmills
Other Versions
Spanish
French
Electric motors have more torque at the same horsepower rating. Here's a discussion of the reasons. March 14, 2006
Question
I've been shopping for a manual sawmill for a few months now. I've tested a couple, looked at a few more in person, and read for countless hours here, and around the net.
So here's my question. I went to look at/test a well known brand a couple weeks ago and the company owner looked me in the eye and said "an electric motor will do the same work as an internal combustion engine of approximately twice the horse power rating."
I was surprised. I thought he might have misspoken. But he said "no, that's right. Not sure why, but it's true. A 10 horse electric is comparable to a 20 horse diesel for example." Is this true? Can someone explain that to me?
Forum Responses
(Sawing and Drying Forum)
From contributor R:
I'd say my 10hp electric below is equal to a 25hp gas.
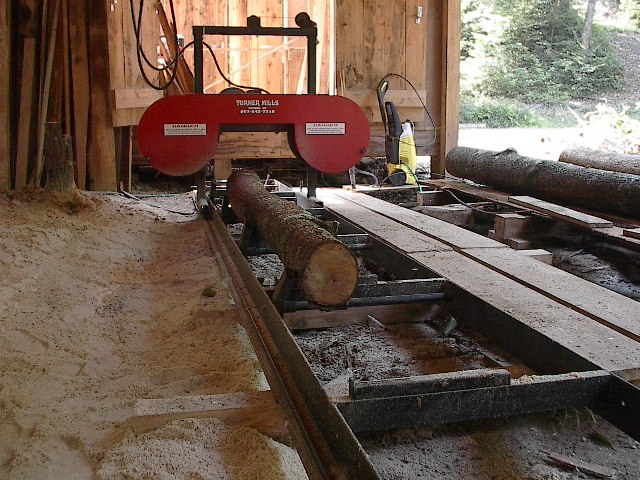
Click here for full size image
From the original questioner:
What makes you say that Contributor R? Do they rate horse power differently maybe? I think I remember someone telling me the "sine wave" of 220 electric was more consistent than 110, so 220 motors provided a more consistent power. I'm thinking maybe that's why 3 phase is a common choice for industrial electric power too, but don't know for sure.
From contributor R:
I think it's about torque though. A 10hp electric has as much torque as a 25hp gas does.
From contributor C:
It's true. In most all cases, a machine that requires 10 hp will require 2 to 3 times more if equipped with a gas engine. I'm not sure about diesel. Diesel I think would be a little closer. Diesels usually have more torque per hp than gas.
Horsepower by itself doesn't really define much. You can have a 10 horse engine that runs at 7000 rpm that won't even cut the grass, or a 10 horse engine rated at 700 rpm that can pull a plow. Both are capable of producing 10 horsepower, but one has much more torque than the other. The leverage that the motor/engine puts on the crankshaft is the torque. To get a real idea of the performance of an engine/motor, you have to consider all three things - torque, horsepower, and rpm.
From contributor I:
Horse power - plain and simple - the more HP the quicker the task gets done. 1hp = lifting 33,000lbs 1 foot in 1 minute (this is how HP is figured). A 1 hp electric motor can raise 33,000lbs 1 foot in 1 minute. A 1hp gas engine can raise 33,000lbs 1 foot in 1 minute. They are equal in horsepower, but may require different gearing to do the task.
Here is the part when other people join in to conflict physics. Horse power – you can't beat it. A 10hp electric motor cannot get the task done quicker than a 18hp gas engine. Output shafts are not equal rpm's. So the gas engine has to reduce the gearing to equal the rpm of the 10 hp motor. That multiplies the torque. And if the 10hp motor geared up to meet the gas engine it would lose torque.
From the original questioner:
So to compare electric to gas I should be thinking "torque" instead of "horse power"?
From contributor I:
If you ever want to go portable by all means get a gas engine. If you’re stationery and live in a quiet neighborhood then and electric motor is the choice. But it might get expensive if you don't have the service to power a high HP motor.
From contributor C:
Contributor I has explained it well. In a simple explanation, hp is how much work can be done in a minute, and torque is how much work can be done in a revolution. The electric motor probably runs at 1750rpm, while the gas at around 3500. Gear ratios come to play here, and the power curve of the engine.
Electric motors generally seem to have a power curve that runs more parallel than the power curve of a gas engine. Gas engines usually drop off fast on the power curve as rpm decreases. So a variable gear ratio would be best suited to make a 10hp gas engine perform similarly to a 10 hp electric. Either way, I agree. If you want portability, go with gas/diesel. If not, electric would be the most economical, dependable, and quiet.
From the original questioner:
It's obvious that electric has many advantages for a stationary mill and that gas or diesel makes more sense for portability. But you then are faced with sizing the motor/engine so as to maximize your initial investment. I'm thinking there must be a "feet per second" of blade travel that factors in too. Do all mills operate within a certain blade speed range?
From contributor I:
To contributor J: If you plan to cut one log per week or even month then a manual mill would work. With a10-15hp engine you could tackle logs up to 24" diameter with ease. A weekend warrior might want to ease the task by having some electrical/hydraulics help by moving the saw carriage through the log and raise/lower the blade.
If hydraulics are present it wouldn't hurt to have more hp. I use a18 hp Honda on my mill. It has hydraulics doing the tasks I mentioned. It takes a while to cut a 27" wide board from oak lets say 2 minutes in a ten foot log. If I had a 40 hp diesel it might only take me 30 seconds to rip the board.
From Gene Wengert, forum technical advisor:
Another consideration is 110 versus 220 versus 440. The higher the voltage is, the lower the current and the smaller and less money the motor is. There is also single phase and 3-phase considerations. This subject has been addressed before and there are some good discussions in the archives - use electric motor for the search terms.
From contributor P:
A gasoline engine delivers its rated horsepower at a narrow RPM range. The horsepower (and torque) drops off quickly outside this narrow RPM range. An electric motor has a flatter HP vs. RPM curve (a wide powerband.)
From the original questioner:
"A gasoline engine delivers it's rated horsepower at a narrow RPM range. The horsepower (and torque) drops off quickly outside this narrow RPM range." Are you saying that as long as you keep the rpms in the "powerband" 10hp gasoline will provide the same hp and torque as 10hp electric?
From contributor C:
Not really. It still depends on the engine and motor being compared. The answer is yes if the engine and motor are both capable of producing the same amount of torque and hp at the same RPM. There will be a point in the powerband where both power sources will be equivalent. The problem is that the gas engine will drop much more quickly when the rpm factor of the powerband is changed.
From contributor K:
I have just purchased a new manual band mill and will be converting it to an electric drive motor for the band saw and carousel drive. When I researched the combustion engine, I was surprised as to the actual fine print (which was a difficult search) about how the engine was tested. The engine manufacturers follow the SAE code standard of J1940. In a nutshell, this test (and of course I stand to be corrected) runs for only 30 seconds to determine the peak torque at max rpm (3600), which they can advertise as the torque output.
They also recommend that the actual torque should be de-rated to less than 85%. Another de-rating from the engine manufacture also comes in the altitude in which the engine will be running. This de-rating is 3.5% for every 1000 feet above sea level.
In my application I sit at 2500 feet above sea level, thus when researching for a 21 hp engine my total de-rating was 76.25%. This dropped the actual output torque rating to 16 hp. I am using a Vanguard v-twin OHV Briggs & Stratton. This info can be found on their website after some digging.
You should also look into the fuel consumption of the engine. I believe the rule of thumb is .41 pounds per hour per hp or .41-lbs/hp hour at 2400 rpm. Gasoline weighs approximately 6.15 pounds per gallon. So in my application I will be consuming around 21 hp * .41 = 8.61 pounds of fuel which is 8.61 / 6.15 = 1.4 gallons per hour at 2400 rpm.
Electric motor torque can be found easily at any manufactures website for comparison. You can compare energy costs easily from the info on the site from your electric bill.
From contributor F:
An 1800rpm motor will produce 3 ft lb of torque per hp running under full load 24/7 with no problems. It takes a much larger gas engine to run under these conditions so that it won't destroy itself. The reason the electric motor will out-pull a gas engine 2 1/2 to 1 is that the motor torque can double its torque for short periods of time. In sawmill conditions where the blade is only sawing 50 % time it allows the motor to cool off from the increase in torque demand. With a gas engine, there is no reserve in torque output, the engine just lugs down and looses rpm.
From the original questioner:
So let me ask this: When you folks talk about this powerband fluctuation causing hp drop in combustion engines, what causes the rpm fluctuation in the first place? Is it the resistance of the wood as the blade gnaws its way through? Is that what makes diesels’ engines better suited to heavy work than gas engines? They have a wider power band and produce more torque at lower rpm’s?
From contributor G:
This is not an easy question to answer because looking at horsepower alone is not a good way to evaluate how any power unit will work. If you look at a saw running at full rated speed but with the blade running free, it is not running at full rated horsepower. It may be running at 40 to 50 % of rated power and it will take the same power regardless of type of power unit.
Now when the blade meets the wood, there is a sudden need for more torque and an electric motor has the ability to respond at the speed of light to call for more electrons and has a mega-mega watt power generating system in reserve to supply those electrons. An internal combustion engine has no chance in the race to supply more fuel (torque) as the carburetor or injection system cannot react any where near as fast. Plus, as the rpm of the IC motor drops while waiting for more fuel, the torque output potential is also lower at lower RPM's (the steeper torque curve) so it is even further limited in its ability to respond. That is why you need a bigger IC engine to compare with an electric motor.
From contributor P:
I think Contributor G just said what I was thinking. As soon as the blade hits the wood (with a gas motor), the RPM's suddenly drop and you are out of the power band. An electric motor, with its wide powerband will not lose as much blade speed when it hits the wood.
From contributor V:
Another component to consider is the energy that is consumed by the IC engine because of the very nature of it reciprocating design. It takes a significant amount of energy to keep the pistons in motion by rotating the crankshaft, thus a reduction in efficiency.
This is why high performance racing engines have converted to light weight alloys and balancing and blueprinting of the reciprocating mass (internal components of the IC engine) to reduce the reciprocating mass, reduce drag, increase efficiency and send more power to the wheels. Electrical motors, by their very nature, do not have to deal with these same issues. The only drag placed on the motor is the rotation of the band wheels and the blade cutting the log.
From contributor T:
It is generally accepted that an electric motor will give what can be construed as horsepower at about 2 1/2 times the rate of a gas engine. It has to do with the electric motors ability to keep its rpm up with a correspondingly high amount of torque over a wide range. Electric motors start up with very high torque, level off slightly under, and maintain that level throughout, if they are overloaded, the torque drops quickly and the motor stalls. Gas engines are usually rated for horsepower and torque at a specific rpm, go under or especially over and the torque drops off.
Because the electric motor can maintain its rpm over a broader range because of its torque range, particularly when pushed hard, it is more likely to keep its rpm up, cut faster, and not stall. I ran my mill 35 hours a week on a 18 horse gas engine, maintained perfectly, broke blades, spent $25 a day on fuel (when fuel cost 1/3 what it does now) listened to noise, and never understood why I couldn't get good production.
I changed to a 20 hp electric 240v 3 phase and I spend about $30 a month on power for everything. It hardly ever breaks a blade, cuts 25 to 30 % more wood with almost no noise, there is no motor maintenance, and you don't need a clutch on the mill. I feed at 55 feet a minute with the blade running 6000 ft. min.
Since I have the power close by, I have lights on the mill for good visibility, and I put air cylinders on my clamp dogs and have a small compressor to run the air. Hydraulic oil is pricy and so are hoses, pumps, and valves.
From contributor F:
If you can get your hands on a Baldor motor book, you will see that the torque increased as more load is applied. The torque can increase to 2 to 3 time’s more than running torque. Baldor shows what they call "break-down torque". The torque can increase to 3 times or more than running torque. A motor produces it maximum torque at stall speed, and this is called "locked rotor torque". The motor torque does not fall off as the load increases.
From contributor T:
I guess I didn't state it correctly when I said that if a motor is overloaded the torque drops off. What I mean is, as rpm drops below a certain point (in effect at the moment a locked rotor occurs) the torque is lost. This happens very quickly and despite what is said in the book you have to see it happening. I have a lot of 600v, 450, 240v 3ph. motors here and the effect is the same, overload it to the point where the motor is about to stall and suddenly the whole process collapses. But an electric motor has a wide torque range, from the virtually from the start point to the stall point.
Referring to the drop in torque with a gas engine, a gas engine loses torque even as it is sped up past its optimal rpm - torque curve. Sorry if I made that confusing but I meant to try and make it clear that a gas engine produces its best torque at a certain speed, as you load it, the rpm changes and so does the torque if you go too far below that optimum operating rage, you can run it past the optimum speed and if you load it to the point that it is operating at its best rpm theoretically everything should be fine, but if you didn't have enough horsepower to begin with you are going to fight this constantly.
The point is that if you have electric available and moving the machine is not an issue, use an electric motor. I have worked on rolling mills with 2000 hp motors and I can assure you that using gas or diesel would never be an option. Every big mill here in Northern Ontario uses electric.
From contributor F:
If you live in the part of the country where there is a lot of power outages, buying a little larger generator to run your sawmill would make sense to me. It could be used for stand by power and also run your mill. There are a lot generators in the 30 to 40 kw size that show up on E-bay. You could run all of your millsaw equipment with one power source.
From contributor O:
I'm using a 65 horsepower phase generator to run my mill, dust collection, and 6 head Danckaert molder all at the same time. Input is 240v single ph. 200amp. A mill alone would not require anywhere near this capacity with a 20 hp. 240v 3ph. motor.
From contributor R:
This is very simple. Gas engines only produce power every other revolution of the crankshaft. Electric motors produce power every single revolution. That is why a 10 hp electric is same as the 20 hp gas. I have two sawmills, one has the 7.5 electric, the other has a 20 hp gas. The 20 hp gas is just a little better that the electric.
The comments below were added after this Forum discussion was archived as a Knowledge Base article (add your comment).
Comment from contributor A:
The answer is very simple. The HP rating of a motor or an engine is given at its rated speed. The rated speed is around 1,750 RPM for an electric motor and 3,800 RPM for an engine. Since HP = Torque x Speed x 32,572 (where Torque is given in lbs-ft) then for a 3,800 RPM 20 HP engine run at 1,750 RPM (equal to a motor speed), it will provide only around 9.21 HP) so at this speed, a 10 HP motor is sufficient. The other point is the difference in behavior between a motor and an engine. The engine gets slower as soon as the torque rises. At the opposite, a motor provides more torque as soon as it speed lowers. This is the reason why a motor is much more aggressive compare to an equivalent engine.
Comment from contributor B:
Electric motors are upwards of 90% plus efficient. Internal combustion engines are 30% to 35% at best. That is another reason for a guideline if you need or have a 30hp gas engine. A 12hp electric motor would be almost the same. 30% of an IC's energy is wasted in the heat from the exhaust. IC engines are terribly inefficient. A turbo is a good improvement as it makes use of the wasted exhaust energy/pressure and turns it into more hp's.