Best Equipment for Tenoning Door Parts
Basic advice on machinery and cutters for making cope-and-stick architectural door parts. August 5, 2006
Question
How are you end tenoning doors? We currently use a bandsaw to cut out the tenons and then use inset cutters on the shaper to cut the negative profiles, but because it's a bandsaw, there is always some fitting required on the tenon.
I was thinking about using our shapers with a monster set of cutters, but wonder if that's the way to go. Can you just use one of those huge shaper cutter sets to cut the tenon and negative profiles all at once? Sounds pretty cool if you don't lose your hand in the process. Or should I consider purchasing an end tenoner?
Forum Responses
(Architectural Woodworking Forum)
From contributor C:
The negative cuts are called cope cuts, the profiled - positives - are sticking. You are likely asking about a cope and stick mortise and tenon joint. Shaper, single end tenoners, and double end tenoners are the three ways this work is done. Guarding and common sense keep the hands intact.
From the original questioner:
Yes, I am talking about cope and stick cuts with a mortised tenon. How effective is it to use the shaper to cut the tenons and cope cuts at once?
From contributor F:
You said doors. If you mean
cabinet doors, then a shaper is the standard tool for making stick and cope (also called cope and pattern) doors. The cope cut (negative profile) and the tenon are cut at the same moment by one set of cutters. The stick or pattern cut is cut by a second set of cutters. Entry doors require heavier machinery than
cabinet doors. Anyway, the straight answer is yes, a shaper is a great machine to use for this process. Very effective.
From contributor D:
I'm thinking you're talking about passage doors, from the question. The cabinet door work has been covered elsewhere.
1-3/4" thick end cuts can be done on a shaper with 8hp or more, and some cutters designed specifically to do end work. The old American iron single end tenoners (Greenlee, Mattison, etc) can do this easily with proper tooling, but they are difficult to change from one pattern to another. The tooling is not common, so tooling companies don't know what you are talking about. CG Schmidt is an exception.
We used to use an old Rockwell/Delta shaper with a stub spindle that would do copes on one face of a rail at a time, after tenons were formed. The stub spindle uses cutters with a recessed lock screw, and the tenon passed over the top of the spindle. This was slow but very versatile, and you had to have your wits about you to keep things lined up. We still use it for some types of curved coping and the odd and unusual.
From contributor P:
What I've done on entry doors is use a shaper to cope the ends of the rails, and a slot mortiser to mortise both the stiles and the rails, and glue in spline tenons. This gives you a faster fitting joint than using a band saw, and, although some recent tests have shown that spline tenons lack the ultimate strength of full tenons, it's probably still enough for their purpose. (I go in at least 2-1/2" on each piece, giving me at least a 5" spline tenon. Depends on the size of the door.)
From contributor L:
We've done lots of them like contributor P with no problems. The loose spline just has to fit very well, glue on both parts.
From contributor K:
We use a large powerful shaper, 1-1/4" spindle and 7-1/2 hp, with a sliding table, to cut door tenons; it works great. For tooling we have 9" diameter aluminum tenoning discs that take standard corrugated back steel knives, which can be ground to a cope profile and do the tenon and cope at one shot. The discs cost around $1k a few years ago, the cutters maybe $150 per set of two. We got ours from Connecticut Saw. I saw a recent post from someone saying Charles C.G. Scmidt had supplied a similar setup. It's a good system but requires a really solid shaper to spin those big cutters safely and guide the work piece through them. By the way, this is one of those topics that comes up now and again - you can save some time and find more responses by searching the Knowledge Base.
From contributor J:
I agree that all the above mentioned methods (and dowels) for door joinery properly executed are acceptable for making quality doors. Double saw blades with a spacer on the shaper is also a low tech method to cut tenons. The loose tenon method is probably the least investment in tooling to set up and good for a shop doing just a few doors. Good dowel construction and shaper – single end tenoning, the middle ground. With NC stacked tenoners, CNC routers for tenons and dowels, and double end tenoners the high end for higher production.
My favorite tools for shaper tenoning are European insert tenon disks. The tooling in the photo is made by Garniga for square edge mortise and tenon on doors 1 3/4” to 3” thick. The set uses double tenons for frames 2 1/4” or thicker. The pieces in the picture are 2 3/4” thick. These are more expensive than the CG Schmidt heads and more versatile. The 250mm diameter tooling in the picture was about $1800 including the matched head to do the end mortising. They are both on sleeves so the height and depth shaper setting is the same for mortise and tenon. Another feature of these heads is adjustable tool holders for chamfering, radius and weep slotting of the joint.
These also require a heavy shaper with sliding table. The Aigner fence fingers can be used up to about a 3 1/2” length tenon. This makes for a safe cut. After that and for tooling 250mm to 350mm diameter, most European shapers have an optional tenon hood and end stop.
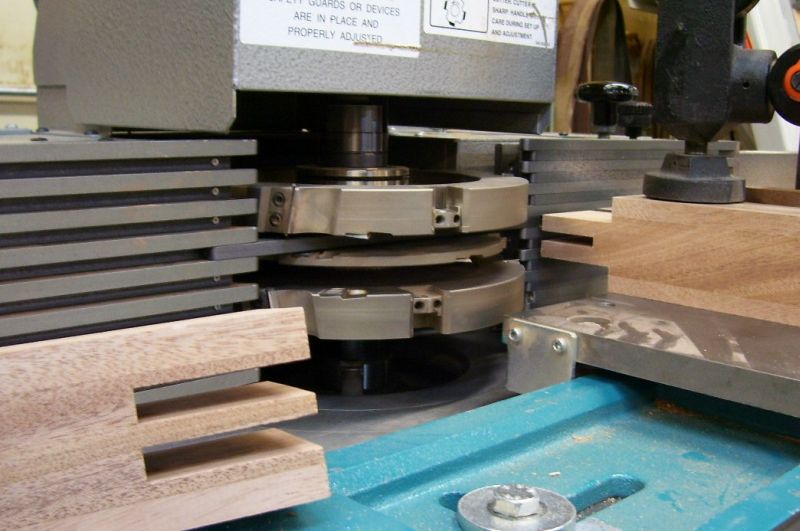
Click here for full size image
From contributor A:
If you were in a real jam, and were really finicky about your miters, you could forgo the cope and stick method, cut straight-shouldered tenons, and apply the profile to the inside of the door. It works really well, especially if you don't have the proper tools.