Building an Entry Door
Other Versions
Spanish
Here's a boatload of advice and commentary for a woodworker contemplating his first entry door. August 29, 2014
Question (WOODWEB Member) :
I've made various cabinets and doors but never an entry door. I'm about to custom make an entry door out of Honduras Mahogany. The door will be 42" wide and 8' high with two side lights for a total opening of about 72". The door will be a simple four panel door and it will be facing east in a porch that sits 6' deep and isn't exposed to much weather (sun/rain). It will be in Alberta (Canada) with extreme cold weather so I have to pay particular attention to weather sealing. My plan was to build it 2.25" thick but my lumber is 8/4 and 4/4 only. So either I'll have to make it stave core (very labor intensive) or perhaps make the rails/stiles from three lamination of 3/4" material. I think to have the panels from two floating panels (inside/outside) with 1/2" rigid foam in between. I'll either use 3" deep floating tenons or maybe 8-10 half inch dowels for joinery.
My questions are:
1. Would a three lamination of 3/4" material be a safe method of building this? What about panels? Is having 5/16"-3/8" tongue at the panels plus 1/2" foam (for a total thickness of about 1.25" for the groove) reasonable or am I better off to make the panels from one solid piece?
2. What finish would you recommend for this? I know wooden doors are pain to maintain in the long run.
3. For sealing the panels, I'm thinking of wrapping all the edges of panels with a weatherstripping foam/gasket before glue-up. What product/material would you suggest for this purpose? Anything else I've missed I should pay attention to?
Forum Responses
(Architectural Woodworking Forum)
From contributor S:
15 years ago I built all the doors in my house with VG fir. I laminated the stiles with three pieces of 4/4 material - big mistake. All the exterior doors warped. Since then, it has been stave core construction with thick sawn veneer faces for any exterior condition. I'm in Texas so we have cool interior with hot exterior. You will be reversed from that. Coincidentally, my doors were all located similar to yours and were the same size. I've never had a problem with the stave core construction.
From Contributor O:
U should incorporate sill/threshold and weather stripping at the door bottom. It seals the door bottom not only from weather but also blowing rain and water wicking up the stiles. Perimeter weatherstripping and jamb details. Do you know about springing a door? Also use sidelight glass sealing and weatherproofing. Codes are also a consideration. That is a heavy door, is it not?
As for your plans, leave your plies as thick as possible when laminating, then face and edge on the big jointer again to true them up, then plane to thickness. Three plies are fine. I have never heard of a case like Contributor S's with everything warping - that is an interesting one.
I am not a fan of stave core since I know my wood and how to build. I have had about 3-4 warped doors in 40 years. I have used stave core only when wood is very expensive or scarce, and it works fine, just more work. I am a big fan of cope and stick mortise and tenon joinery, with integral tenons on rails - half the joints to make and potentially fail. You don't mention the edge profiles, if any. Integral sticking, applied rabbeted molding, or square edge?
From Contributor O:
Just as there are no thresholds to entry into this profession of woodworking, there are no thresholds into the various branches of the profession. It is probably good that we no longer build airplanes out of wood. I have found that this is often client driven, in that a client that sees a person make a vanity assumes the same skills can be applied to making flooring, building a house, or making a boat. Wood is wood, how hard can it be? This is responsible, in part, for the great cheapening of our craft that has relegated most of us to trying to explain why our work is better than Ikea.
Of course, this ignorance of craft - on both the end user and vendor's part - is neither of their faults, it is unfortunately now the way of our culture to ignore the makers of things and celebrate the makers of celebrity. I wish I had kept track of all the calls and all the doors I have had over the years to either replace or price a replacement for a door gone bad. "He said he knew how to make a door...." The trouble is, that after the fact the customer was angry they had to spend more money, and more money than the first time, and yet they regarded me with suspicion that perhaps I also had sold them down the garden path. It takes many years of finding one's way to resolve those details into a workable, well-performing unit that satisfies all the requirements. There is not one solution for every shop, nor is there a fool-proof answer to most of these questions.
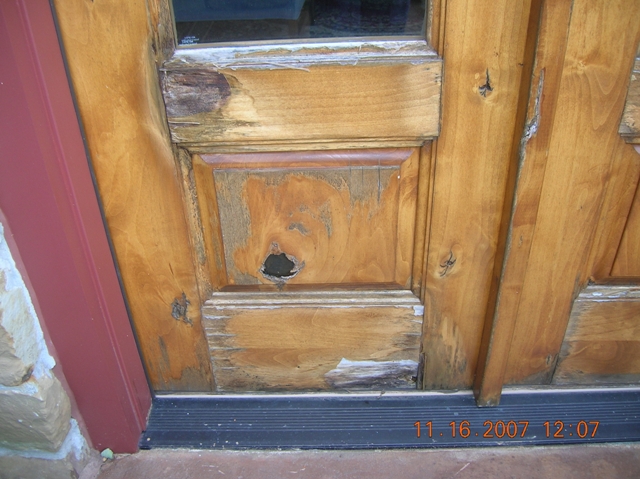
Click here for higher quality, full size image
From Contributor O:
I omitted mentioning that the original poster may well have the skills and resources needed to deliver a good product, and I meant no disrespect by my digression into other areas. My point was that instead of a woodworker determining to learn about and gradually enter a new area, they are thrust into it by a request from well outside that area.
From the original questioner:
I have found a local supplier of door bottom, threshold, and weatherstrip sealing. The local glass supplier who is building the side lights also provides the seal for them. There is going to be four good quality (ball bearing) hinges on the door. Certainly making it out of three ply is easier than stave core but I prefer to do the extra work with the assurance that it has more chance of staying flat. The customer doesn't know about 1.75" or 2.25" thickness and it appears all suppliers of doors/parts around only know about 1.75". So I'm leaning toward building it at 1.75". My wood is 2" or thicker (2 1/8" or more) and I'm thinking I can make it out of solid instead of multiple ply's or stave core. The wood was brought in from another shop that had it in their shop for eight-ten years. So I expect it to be stable and it has been in my shop for a month now. That said, if I decide to do 1.75" thick door will it be fine to just do solid stiles or better off with stave core?
From contributor A:
We used to rough cut the stiles. Face them, don't bother planing them. Let them sit for a day and you will know if they are stable. They will bow if not a good piece of timber. I've made 50-100 doors out of solid non laminated wood (mostly SA mahogany). I've had more problems with ladder framed doors with thick veneers.
From Contributor H:
Same species three ply works for 2 1/4” doors but I would not build 1 3/4” doors with this method. Two critical things to remember when building this way is all plys must be the same MC and you need to alternate the grain direction of each ply. Not doing this will cause bowing. Rift and quartered will make for more stable construction but most Honduran mahogany we get is plain sawn. We also edge glue the middle core to add stability and get better use of material. Sometimes on large doors we do the center core from white oak ripped and turned so as to be quartered or rift to add strength and stability. See picture, the two on the left are interior doors. We use the 3 ply method mostly for our thicker 68mm and 78mm Euro doors and sliders. It makes for a very stable stile at that thickness.
One big advantage of this method is no glue line to the weather like conventional stave core construction with thin skins. On Euro doors the glue line is hidden in the rebates. I also would not be afraid to use solid Honduran mahogany for door stiles. You could build this door 1 3/4 but that is pushing the limits in my book for a door that size. If your 4/4 material is flat sawn you could make a stave core like the one in the second picture. Your exposure sounds pretty well protected so the thin skin to the weather should not be a problem. Stave core has been around a long time. We have 100 year old doors in our town that were built that way.
Building exterior wooden doors and windows is risky business especially in this era of low quality timber and tighter, higher heated and cooled homes. There are many good arguments for using wood though. Many things have to come together to build a quality door. It takes many years of experience, training and tools to get it right. Of course we all had to start somewhere. Your exposure and materials sound good and that is a big part of the battle. Good materials, knowledge of local conditions, good tooling relates to finish durability and dealing with moisture, hardware. Finish, caulking and gasketing has to work together for a tight seal and to let the door breathe and expand. The corner joints are important and the methods you listed are fine.
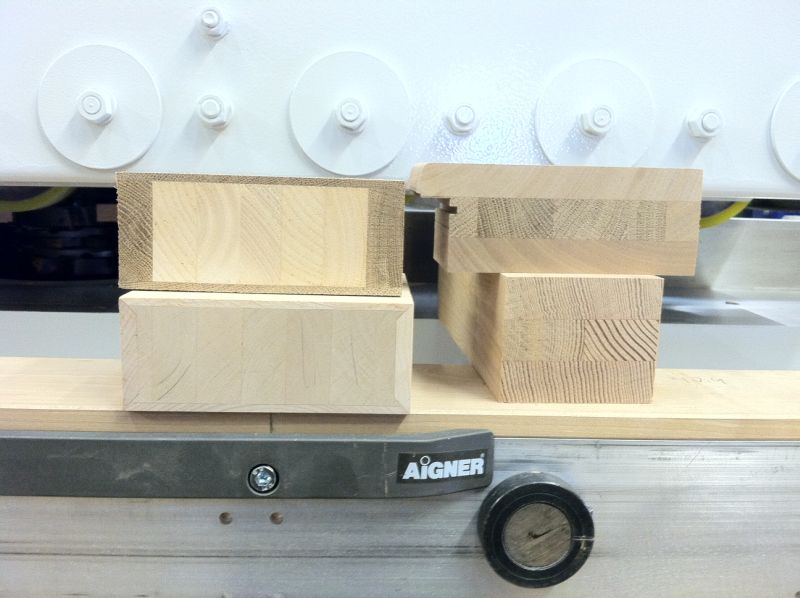
Click here for higher quality, full size image
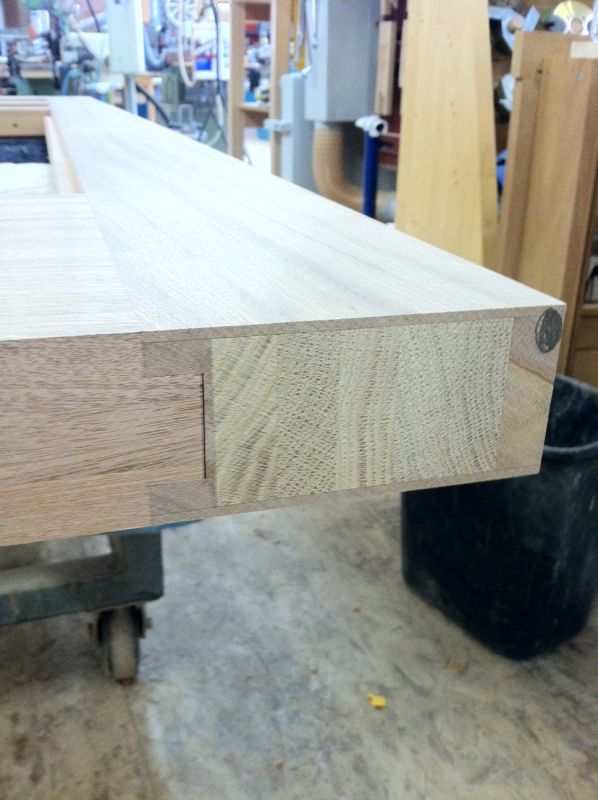
Click here for higher quality, full size image
From the original questioner:
When you say 1 3/4" is pushing the limit is it with solid wood construction or even with stave core (for both rails and stiles) you think 1 3/4" is not recommended? Sourcing hardware/weatherseal material for 2 1/4" thickness has been tough. Will two floating panels back to back in a 3/4" groove be better than one solid panel?
From contributor T:
On a door that’s height goes 2-1/4" thick and I would recommend a stave core construction. For the mere mortals it is totally acceptable, you will be satisfied with the end result and will be very stable. The 2-1/4" thickness will allow a heavier panel and tongue and I would float the two as you thought, use good panel glue up technique. Seal the panel end grain before installing and of course allow room for expansion. We use a firm rubber block to keep the panel centered similar to "space balls". Most decent hardware can be had to accommodate a thicker door you just have to order it that way. Beyond that it is not rocket science, have fun with it. Personally I have seen some exquisite doors built by complete amateurs and some of the most hideous by seasoned door shops. If you are a dedicated craftsman than it will be fine, if not, then it won't matter if it is your first door or thousandth!
From Contributor D:
I use hot melted paraffin wax to seal the edges of my door panels as well as the bottoms of the doors. I no longer assume the painter/finisher will seal the door bottom. I keep a hot plate with a pot of wax and a foam brush handy in my shop. I've learned however to do the door bottom before final sanding though as sometimes it will flow over the edge and require some scraping and sanding to ensure proper finish. I also use a 3 ply, same species, construction for stiles. I have also built many doors with one piece stiles. If the wood is good and dry and flat (face jointing is a must) I have not had trouble.
From the original questioner:
Ok, it will be 2.25" thick and I will use stave core at least for the stiles (probably rails too, or maybe just 3-play for them). Sealing the end grain with wax seems like a good idea. My next question would be what type of finish you'd suggest that lasts a bit longer and is easier to maintain? Also, for panels that are floating back-to-back (with a 1/2" of foam in between) I suppose I should apply the same finish to the back sides of each panel before assembly?
From contributor H:
I have worked with Mahogany many times - if you are going to expose it to the wet you need to seal all the end grain with CEPS - "Clear Epoxy Penetrating system". It is what all top end boat builders use.