CNC Dust Collection Connections
Dust collector hose joints that move a lot are subject to wear and failure. Here's some insight into the problem. April 21, 2007
Question
We run a Busellato Jet 4002XL. The dust collection hose is 12" in diameter coming off the top of the head. Since our machine has a 14ft working area, the hose travels back and forth all the time. We use a high quality hose, but it fails regularly at the top of the head. How do those ball dust collector hookups work? Our dust collector engineer says that we will have as many problems with the ball end as we do with the hose.
Forum Responses
(CNC Forum)
From contributor K:
I’m going to assume a few things.
#1: Your main trunk line to your dust collector is larger than your feed pipes to your machine.
#2: You are using a plastic type "flex hose" to connect to your machine from the trunk line.
Check the following.
- The hose works best if it's attached to an elbow coming out of the side of your main trunk line (obviously pointing down).
- Do not permit too much slack in the hose.
- Position the hose/elbow joint to be as close to the center of the machine as possible. (This reduces slack.)
We have a similar machine and it doesn't have any problems with the hose/trunk connection.
From contributor C:
I agree with the above in every aspect, especially with the plastic flexhose. We were using a fabric type hose previously and it, too, failed all the time. Make sure your hose is plastic.
From contributor A:
2 1/2 years with a ball end type fitting, 12" diameter urethane type hose has worked flawlessly with no replacement needed of either part.
From the original questioner:
Contributor K, your assumptions are correct with the exception of the amount of slack. Our maintenance people ordered extra length to allow for a couple of failures; cut bad off and reattach. When we did have minimal length, we had problems with the force of the dust collection and the weight of the hose pulling the head and requiring recalibration. With the length we run now with the dust collector on, the hose is straight from top to bottom connection and only sags when the dust collector is off. Our hose is about 12 to 14 ft long and the top connection is about 8ft from the bottom. More room between would lessen the angle, but we're limited on ceiling height. We probably have more dust collection power than needed, but usually more is better. I think the ball end would keep less angle at the top of the head, but need to convince maintenance to try it. Remember, our dust collection engineer recommended against it. I hope to use your experienced opinions to convince them.
From contributor K:
I spoke with our CNC operator this morning and brought up your concern. Apparently, one of the reasons we may not be experiencing the problem (or I was not aware that one existed) is that they do regular maintenance on those fittings as part of their equipment maintenance. So in other words, we too would have the same problem if no one checked it and maintained those fittings on a regular basis. (Just goes to show you I'm more of an office guy!)
From contributor L:
We have a Busellato Jet 6000XL.The machine has a 16ft working area. The dust collection hose is 12" in diameter coming off the dust collector with a 90 degree bend downward. We then put a ball swivel and hook up the flex hose top of the head. Our hose fails at the top of the head approximately every 18~24 months. Because of lack of ceiling height and back wall depth, it would do us no good to put a ball swivel on the router. I have considered a roller track with a strain relief to lessen the stress on the hose, but have not gotten around to it. I too would welcome any good ideas.
From contributor D:
I have a similar situation (no ceiling height). I have thought of the track as well, though have never got around to it. What I am currently using is a long rubber bungee with an eyehook screwed to the ceiling. The bungee works well and supports the hose when there is extra slack; it also stretches when the hose moves around. Just a simple fix.
From the original questioner:
Have you ever tried the ball swivel at the top of the head and not at the elbow down? Has the ball swivel given you any problems? Ours is failing about every 4 months, sometimes less.
From contributor M:
As you can see in our setup, we have a swivel at the end of a straight length downstream from the machine. Long straight and short flex helps keep the static pressure up. The straight pipe rides on the horizontal beam smoothly. I am not an expert, but ours work fine. After 3 1/2 years one shift, we haven't replaced any hose from movement, or rubbing, just wear and tear from wood chunks hitting the hose and booster fan assy.
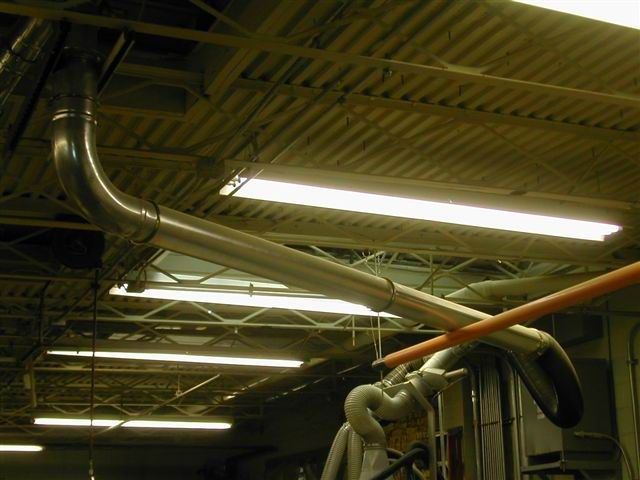
Click here for higher quality, full size image