Cultivating Initiative and Creativity on the Shop Floor
Here's a thoughtful discussion about how a shop foreman can train his employees how to think for themselves, rather than simply solving problems for them. Also mentioned: how to craft shop SOP's. February 11, 2010
Question
Lately it seems like every time I try to start my own small project, someone interrupts me with a problem and "needs" me to solve it. When I take a look at whatever it is that they need, it ends up being what I think is a fairly easy solution. I don't mind giving input and help every now and then (it’s part of my job as a foreman), but it seems like no one wants to think for themselves. There's an overall attitude of, "I have a problem - what are you going to do to fix it?" It's become such a problem that my own productivity has gone down. What do I do?
Forum Responses
(Business and Management Forum)
From contributor S:
The answer to your question is very simple: you are the boss and responsibility is yours. Nobody wants and will take it from you, because they don't know if you are going to like their creativity and/or decision. In most companies, Forman is not working on any jobs himself, but doing exactly what you have described: making sure all the problems are solved and anybody else is productive.
From contributor K:
I'm a certified designer in the Los Angeles area and used to be a shop foreman. Your function in the company is to solve problems. Employees should come to you instead of making the wrong decision that results in mistakes. Side projects should be worked on after hours.
From contributor Z:
You are needed to do what you are needed to do. If you don't like doing it then give up your foreman’s position and become just one of the crew. Another option is to go out on your own. You'll only have yourself to worry about. You most likely have to be foreman for your ability to solve problems and keep things moving. It should not annoy you.
From contributor D:
If this is a production shop, then you need more intensive training for the employees, and a 3 ring binder (as in McDonald's). If your shop is the type that does a broad variety of work, with various methods and means available, then it is correct that they come to you. However, if it is part of your job, you can help solve your problem and create some empowerment in your co-workers by requiring that when they wish to present a problem, they must also have at least one viable solution, preferably more than one. Then you and he/she can quickly review the facts for the preferred solution, and then move on. This is how problem solving is taught. The side benefit is that people that can handle this kind of empowerment will flourish and feel better about their job - they have some input and direction in how they solve their problems. As confidence is gained between you and your co-workers, the smaller things will solve themselves. You may wish to dedicate 10 minutes at the start of each day to problems and solutions to formalize the time and context in which they are presented. This may also help teach some planning for your co-workers and solve things before they become a problem.
You will have fewer interruptions and inter-shop relations will improve. If someone just brings up problems or likes to bug you, then they have directed their future. We call them 'former employees.' If there is someone new, then they can be paired with a more experienced problem solver so they learn the benefits of thinking for oneself, for the betterment of all.
There are some that will feel this is a 'set-up' as one guy once told me. They are slow to catch on, but if they become trusting and their input is valued, then they turn around a nice 180 degrees.
As an aside, the fact is that problem solving is not taught in our schools now that we have moved to a service (taking orders) based economy. In fact some schools look at 'thinking for oneself' as a problem or threat. This is how we end up with a government that resorts to force for problem solving, and we have individual leaders that are not sharp enough to even pull off an extra-marital affair.
From contributor N:
To all, it's not the problem solving that I'm annoyed with. It's simply the fact that no one can think for themselves. Contributor D had a great point which cuts to the heart of the matter for me. If you have a problem, don’t just come to me with a problem and ask what to do - tell me the problem and what you think you can do to fix it. In my opinion, it’s always better to have more brains figuring it out. Maybe someone else has a perspective that I hadn't thought of straight away, or perhaps the circumstances call for something that one of the other employees knows more about. Like I said, it’s not the problems, it's the lack of any thought from anyone else.
From contributor F:
Simple replies you can make: "How would YOU solve this problem?" "You just asked me that a month ago. What makes this situation different?" "I really expect someone with your experience and pay grade to be able to solve these type of problems yourself." To be a good leader, you have to have some tolerance for occasional failure from people who make an honest effort to excel.
From contributor K:
A foreman is a babysitting job to some extent. It comes with the position. Asking what they would do, usually works. They already know the answer, but want to make sure most of the time. Maybe you chew them out to bad when they do make a mistake? That would make them a little uneasy about making a decision.
From contributor G:
Just to underline what contributor D said as his remarks are right on the money - make them come to you with a solution. Most workers want to be able to control their work, so show them how to do that. The current culture has a severe dearth in this department.
From contributor J:
My first boss in milllwork was an old school hard ass. He was a genius at the work but intolerant to the extreme in being bothered with questions if you already had the answer at hand, but just had not looked hard enough to find it. It was a rare and quiet victory to bring him an issue with a project that he could not burn me with by finding it in the notes in my hand. I saw his end of it years later as a foreman plagued with guys that would halt and distract me with pleas of "Where is the .....?" and in response, I could look around the shop without taking a step, and tell the lost puppy " There it is, I can see it from right here, find it yourself."
From contributor U:
One of the things that differentiates western manufacturing philosophy is the premium we place on personal initiative. It's not uncommon to hear the mantra: "If you can't figure it out come find me, but I expect you to try ..........." What has just happened here is that your least experienced person is now in charge of corporate policy. If he or she can find a work-around that satisfies them, they don't need to involve you. In fact, they are specifically instructed to only involve you if they fail. With this mandate it is no wonder that it is such a struggle in these shops. My hunch is that we already spend the money it would take to develop proactive work instructions, but we spend it on mopping up bad decisions or excess overhead because things take way longer than they should.
From contributor U:
Of course there has to be some kind of strategy in place for people to know what to do and how to do it. My contention is that for most of us that strategy is somewhat informal, and I suspect not actually written down at all. Here's an example of something I am working on right now for my company. At the most basic level this represents a storyboard for an eventual video training presentation. All management is list management. The list can be something you keep in your head or it can be something that is written down. If you write it down on piece of paper you have to find the paper. If the list is electronic others can find it as well. In this case you can see that the simple act of mortising a cabinet door has 21 discrete procedures (there are probably more).
Approaching this formally gives us the option to understand where we can lower costs and monitor status. The tasks are color coded by skill level. The obvious goal is to turn everything yellow. Bright yellow serial fields indicate the presence of a memo or nuance. Green fonts under the part field indicate there is a suggestion for improvement on the memo layout. Is everything is assigned to a workstation you can eventually do a sort by workstation. This is the foundation for developing a training program.
What is the best method for chiseling the corners square on the hinge mortise? Task Number 11 should be fully vetted and not left to the discretion of individuals. Particularly if your method of training is for newbies to just randomly observe and learn by osmosis. Kind of shocking to see that just the simple act of getting a door mortised and hung takes 21 steps. But there it is. You can see it.
You can now assign a location, method and sequence to the procedure. You can measure non-value added transport between procedure to procedure. Our work day consists of minutes. A minute spent walking costs the same as a minute spent mortising. If you can collapse 21 processes to 16 processes you can probably go from 60 minutes to 45 minutes. With proper systems what used to take a $20 guy 60 minutes to do can probably be done by a $15 guy in 45 minutes. If you accomplish this your direct labor costs go from $20 to $11. That’s just from watching minutes. That's what is called a durable advantage.
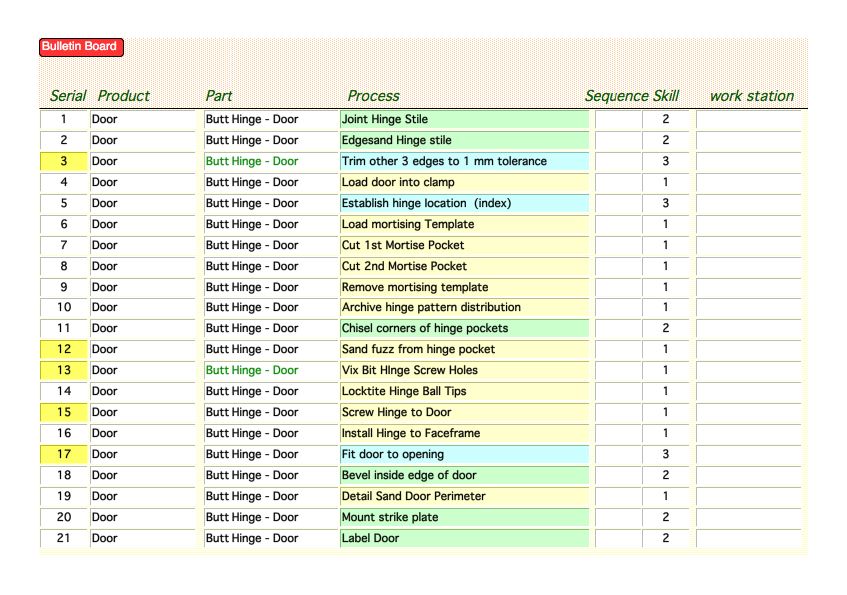
Click here for higher quality, full size image
One more thing: this type of strategy is not intended to eliminate the need for craftspeople. If anything it is a method to free up craftspeople to focus on problems that need solving.
From contributor D:
Color-coding, charts and three ring binders all work well - are necessary - for the production shop making the same/similar widget every day. Those tools diminish markedly in a shop where ten people are working on four different products, all with different materials, methods and skills. It is likely that a percentage of the projects that come thru such a shop will have never been done by the shop before, or are of a complexity that begs for different management solutions - or even information management solutions. This example is the rare duck, I understand, but provides some insight into how first level management, problem solving and productivity all work together. This type of environment is so completely different from the production shop that it does require many individuals to work independently and resolve individual problems with the tools, resources and knowledge at hand.
From contributor U:
So do your people just know how to do these 22 steps when they show up or do you just have your highest skilled guy do everything because it is simpler that way? Does everybody just do things their own way? Does the baton ever get dropped during training? You don't have to color code anything. You can write it on the back of a 2X4 or keep it in your head. How you manage your list is up to you, but you're still managing some kind of list. Think past the list and think about the reasons for the list, or maybe the benefits of the list?
From contributor S:
When somebody is hired it is assumed that he knows how to mortise a hinge in to the door. And like contributor D said, those charts work well in production environment with low paid low skill, or no skill labor, but not in custom shop when every next job is different. Instead of color charts on the wall, there is foreman in the shop.
From contributor U:
I am sure we have all had situations where there is a difference of opinion as to the best way to do something. I think there are a lot of times also that a new hire receives contradictory instruction, depending on who he gets his training from.
Take that mortising operation, for example: I would bet that the big boys use a spring loaded corner chisel to square out the radius from the router cut. I'm equally certain that some would swear by a really sharp chisel. Others might score the material first with a combination square and utility knife. We can all agree that the first two methods are in wide currency. These two methods, however, couldn't be more different in approach. What is the best method here? Would something like this not be worthy of discussion before you send your foreman out to the shop to establish best practices policy? For as much whining as we are hearing about the economy, I would think that discussion of best methods would be of at least some merit.
From contributor T:
I believe at the top of this thread there was something mentioned about creative thinking. I tend to agree that there are fewer free thinkers to go around because we are relying too much on computers to draw for us, cut for us, and even assemble. Our industry needs people who can think and design so we don't have to get bored with our existence. The way some shops are set up, we stifle thinkers because we need them to just follow the rules and nothing more. In some cases the people we hire are only good at doing just that.
Our shop has systems in place for doing various functions, and they have been done like that for many years. We recently hired a new employee, showed him the process we use to get our products out the door, and set him to work. My employees know that being a design oriented company we will always listen to their ideas. The new guy was given the task to make up 60 sets of legs for a computer lab we were doing. After the first five sets he figured out a better system and took it upon himself to implement it. We now have more space in the shop, and the legs get done about 25% faster because of a creative thinker. We don't have any handbooks or charts and we don't have meetings and recently no foreman (not a creative thinker). This is just my way of doing things and I do understand peoples need for order, but at what cost?
From contributor G:
To contributor Z: how do you allow for improving the system?
From contributor Z:
Continuous improvement is all about creativity. Everybody wants problem solving in their day. The trick is to get people to solve problems that need to be solved. I would rather have my talented people developing a new line of a product than applying labor to mop up an out of sequence process from something we should already have dialed in with surgical expertise.
How about focusing instead on developing a furniture foot for a kitchen island that can be installed on an out of level floor after the floor has been finished? To complete the loop we will need some way to get the customer's endorsement of the design. We will need an elegant way to fabricate it so we can get it built and we will need a way to explain it to the installer so the trainwreck doesn't happen at the jobsite. These are problems that need to be solved. There are more just like it. Minutes that we spend being stupid are minutes that we can't spend being creative. There is a finite number of minutes available in the budget before the project starts to go under water. By the way, was your protégé allowed to just implement this new great idea on his own or did you have a system for approving changes to the program?
From contributor Z:
Last week I worked in the drawer box department with my daughter. Together we changed our system for assembling the parts. Our new method is substantially simpler than the old one and takes about half as many minutes. This was a problem worth solving.
We do not have a formal way to petition making a change in process. In this case I ran the idea by me and decided it was for a good cause and worth the expense. The next step will be to put it onto a storyboard then make a video of it. The video, (similar to how a golf pro teaches people to correct a swing) will show us what we can't see while in the moment (like amplifying non-value added excess motion). We will use the video to discuss what we learn, tune the process up and re-film. I think we can lower all of our costs to 1/3 of what they are today (notice that said costs, not minutes).
From contributor S:
I vote for creative thinking, not replacing it with ruling authority of no thinking. To me it really does not matter how cabinetmaker mortises the corner, as long it is done efficiently. I would use hinges with round corners, if I can, and completely eliminate 21 steps. I believe in no charts, but instead in human talent and creativity. I think charts and standard procedures, lock-up challenge, kill any desire to be creative and in the end we have lifeless product.
From contributor I:
For the original poster I have to agree with the majority here. You are the shop manager and it is your job to give direction. If you express the attitude towards your employees that you are expressing here, you are not a good leader. Managers are leaders. In your defense if the shop has no standards and no defined procedures for making your product your job is a lot more difficult than it should be. I suggest that you get the AWFS and take some courses on production. Or read some books on the subject.
Those who claim that custom cabinets cannot be standardized are closed minded. I build extremely off the wall stuff and it is still standard production 95 percent of the time. All your boxes can share the same construction. Adopting standard depths in sensible increments is a huge help. I know the 32mm system is a touchy subject with the "my shop is too custom" crowd but it adds a high degree of standardization with plenty of room for even the most off the wall designs.
Just standardizing drawer heights and stretcher to slide-boring-pattern saves tons of time and mistakes. No matter what the pattern never changes and we have a dedicated machine for that job. It bores the slide mount holes and the dowel holes for the stretcher in 20 seconds including pulling the part and stacking it when done. All we have to do is move the stop to set the distance from the top of the panel, and that is restricted to 32 mm increments. Bam! It is idiot proof. No one has ever asked me "How do I set up for this drawer?" or "What is the dowel pattern for this cabinet depth”. Don’t fool yourself into thinking you are doing the best you can do with what you have. Nobody is. Keep improving.
From contributor S:
Dowel pattern never changes, that is right. But shelf holes do. Some customers do not want to see holes that close, so I try to move them to 64 instead of 32 so CNC router plunges group of the bits instead going one by one if non standard pattern is chosen. But I don't have to always set the holes 37mm back from the edge of the side, so shelf holes also accommodate hinges. All those standards are well known and used. Honestly, I don't care if holes are not set in 32mm increments, or dowel pattern changed, that is all done on CNC and is drilled automatically anywhere I place the hole on my drawing. So the depth of the cabinet, any depth is fine, it is nested and cut on the computerized equipment, why it matters? Anything else besides boxes is millwork, never repeats, never looks the same and was never built before. Well, yes, there are standard procedures to some extent, how to attach the face frame to the box or how to mortise the hinge in to the door stile, but again, techniques may vary from job to job. Some are in this business to build simpler staff, more staff and as much as they can, and charge as little as they can, and some do not want to do that. They build unique, they build less, and they try to charge more for it. That is the matter of choice.
From contributor T:
In my way of thinking, I do not want to build cabinets using the 32mm system or standard building methods. When we went to building custom furniture/cabinets we designed things that were far from standard. We all make choices as to what we want to make and how we want to make it, which also means we are not wrong. If an individual shop gets all kinds of systems in place, to build what they choose, that doesn't mean it will work the same for my shop. We all have different sized shops, different tools, different designs, and the biggest difference of all, boredom. It is possible that some companies do not have being the most efficient shop on the planet as their goal. I want to enjoy what I do, I want to have fun doing it, and I want my clients to like what they get. If I happen to make some money along the way then it would seem I am heading in the right direction. If that is wrong or if that makes me an idiot then so be it. I think that a creative thinker is anyone who can take the jumble of ideas, materials, people, and make it work. Building the same thing day after day takes commitment, but so does building art.
From contributor D:
Well said. One thing the field of woodwork has is diversity. Not everyone builds cabinets, and fortunately, not all of us have fallen for the 'new' meaning of custom that is not really custom at all, or where custom is only within a narrow range of otherwise very normal details. 'Custom' as a descriptive word is more abused than 'high end.'
The designers and buyers of our work dictate what details we will incorporate, and they most certainly do not want their architectural woodwork to look like it came from Ikea, or from Ikea with an Enkeboll carving plopped on the front of it. They rely on us to not only work within their details, but also to add our own that will make the work stand out in all manners of criteria. This goes well beyond the narrow notion of adding value where one or two things are slightly puffed up sufficiently to stand out - just a bit- to make the product appear better in the marketplace. We just do what other people won't/don't/can't do, and we do it well, without whining or complaining.
Talk about boring! There is that old joke about a boring machine, in more ways than one, eh? While it is fine and dandy to split hairs over this method of driving screws or that method of accounting, I would prefer to spend my day with the things that interest me. That type of work would kill me in a week. I'd rather sell life insurance. If someone else wants to detail the details endlessly, I support them 100%. There is no end to that, so there is some sort of job security, but it may not be for everyone.
What interests me and the people I work with is building things in creative, proper and pleasing ways. What are our options for this assembly? Let’s get together and figure out the best way to make a batch of 11' long tapered, fluted columns. How would we hang these doors with what kind of hardware? We are all solution junkies, and I'd have it no other way. The money follows, and the business can grow as fast or slow as we want it to. The point is to build a base that gives a good living to us all, provides a higher level of product and service than most people are accustomed to, and have more than the normal job satisfaction along the way.