Drafting Hours per Dollar of Cabinet Product
CAD pros kick around some ballpark draftsman productivity numbers, and discuss the factors that affect efficiency. August 8, 2008
Question
Does anybody have a standard number for drafting hours per job or residential versus commercial? Do you field dimension prior to or after the submittal process?
Forum Responses
(CAD Forum)
From contributor M:
That's like saying, "How much for an average size kitchen?" Well, um, hmmm, don't know. We need more details than that.
From the original questioner:
I am actually looking for a general answer, for example, 1 drafter per so many cabinetmakers/labor hours. As far as what we do, custom residential, radius diewalls, commercial plam - we hit the whole spectrum. Currently we use Micro-Vellum, AutoCAD and e-cabs... Submittals are done in either AutoCAD or MV.
From contributor G:
I too would be curious about this. I want my department to start tracking our hours, and I want to see where we fall in the range.
From contributor Y:
In South Florida for high end residential we typically use the equation of $1000 = 1 hour of drafting. For example a $50,000 kitchen will take 50 hours to draft. Now this works as an average equation - it all depends who is actually drafting and the speed and experience that person has. Keep in mind these drawings need to have a standard look to match the quality of the job which typically is more detailed than a commercial job.
From contributor A:
Is this a number based on you drafting? If so, I'll make my own equation, 1,000 dollars = 2 hours of my drafting ability... LOL.
From contributor Y:
Actually that number is for an above average drafter. Someone that knows what they're doing but he or she is not the fastest pistol around.
From the original questioner:
1000 per hour seems about right. We can use MV to generate a row of base/upper cabs with sections pretty quickly. However, the process of submitting and revising seems to gobble up a lot of time (changing cab sizes on the drawing takes as much time as drawing it), not to mention spacing it out and printing it all over again. Is there a process or technique to avoid this?
When drawings are returned "approved as noted," i.e. begin building, do you then redraw for the purpose of the shop floor or work off the redlines?
From contributor Y:
When you use Microvellum or any other AutoCAD related software to draw the cabinets, you should always consider the possibilities of an architect's red-lines. Of course pending on the level of the red-line revisions you spend more or less time resizing and moving cabinets around, but it should not take as much time to revise the drawings. Microvellum makes it easier to revise the drawings when you keep in mind how the cabinets are moving around the model space. You can resize many cabinets at once (when you use the 2D mode) by using the "move and stretch 2D products" under the "product" menu.
As a process to avoid spending extra time revising drawings: learn how to use the paper space to set up the submittal drawings; that can save huge time when it comes to revising and reprinting the whole project, since you only have to set up the submittal pages once.
As the "Approved as noted" stamp. Again pending on the level of the red-lines and if it affects the machining of the parts, I always apply the revisions prior to sending the drawings at the shop. Sometimes we avoid the drawing changes if the red-lines are very minor and we urgently need to send the job for building. But keep in mind it is always better and safer applying those changes on the drawings no matter how minor the changes can be to avoid confusion at the future.
From the original questioner:
"but it should not take as much time to revise the drawings. Microvellum makes it easier to revise the drawings when you keep in mind how the cabinets are moving around the model space."
I have resized cabinets often in MV and always find myself resizing then moving the cabs around to get them lined up again...
"You can resize many cabinets at once (when you use the 2D mode) by using the "move and stretch 2D products" under the "product" menu."
I will try this.
"learn how to use the paper space to setup the submittal drawings; that can save huge time when it comes to revising and reprinting the whole project since you only have to set up the submittal pages once."
I don't understand this... I use paper space for submittals all the time, but I still need to make changes in model space regularly.
We did a process analysis and found that the drawings are being done 3-4 times prior to building:
1 Initial (gets reviewed by project manager)
2. Revise off of PM's redlines
3. Submittal to client
4. Revise client's redlines
5. Build
Is this the lean process?
From contributor G:
I'm finding this thread more and more interesting because this morning I went into work with the sole purpose of wrapping up my drawing template improvements and detailing blocks. I really think your outline above is what's necessary for the comprehensive communication that shop drawings are supposed to be. In my position, I'm the Senior PM, but also head of the engineering/drafting (small, 4 person dept). I think it's absolutely necessary to review the drawings before they are sent for submittals. I find I need to print them out, take a breather, and switch gears to see the things I missed when I was drafting. (I often take them home to redline.) It's too tempting to just think you're done and send them, especially when you're behind schedule. I've learned the hard way, and that's why I'm revising our methods.
I would be very interested in hearing anyone else's processes, especially if they're working in MV. For example, I had never used the command contributor Y is speaking of either (2d stretch and move), but I just tried and can see how powerful it is.
From contributor S:
A good draftsman will prepare approximately $10,000.00 worth of cabinets in one hour for production (for CNC or ?). He must use Cabnetwork or Cabnetvision or any good professional software. Your parameters must be set up perfect.
From the original questioner:
1K per hour, not 10K. Getting the drawings done, yes. As far as printing reports, labels, ensuring CNC output is correct, etc... figure two hours.
From contributor S:
10k - okay, not one hour, but 1 1/2 to 2 max.
From contributor Y:
$10,000 of drawing/cabinetry in 1 to 2 hours cannot be considered average. What market are you in? My equation numbers come from the custom high end side of woodworking. I attached some drawings to see the level of details we put in these projects. Of course commercial jobs do not require this kind of drawing, but the numbers should be similar when you consider the price difference in high end residential vs. commercial.
Per your numbers, if in a week you put in 40-45 drafting hours of work, that means you output a minimum of $200,000 per week and if you consider the yearly output of 200K x 51 weeks = $10,200,0000
Now you can tell me you do not put 40 hours a week in drafting because the work is not there, but I know companies that have plenty of work with 3 full time draftsmen and output maximum of $3,000,000. By the way, these companies use similar equations as the one I stated above. The numbers I gave did not come from just me but several people I am associated with and work in the high end market of South Florida.
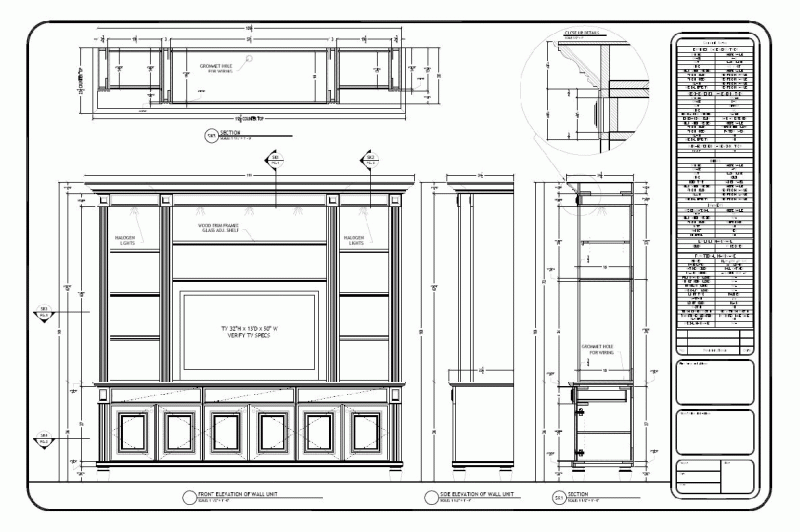
Click here for higher quality, full size image
This is page #2 of the same project. These drawings were finished using AutoCAD/Microvellum and all the manufacturing data is included. The number equation I gave on top (1K=1H) is somewhat valid with this project.
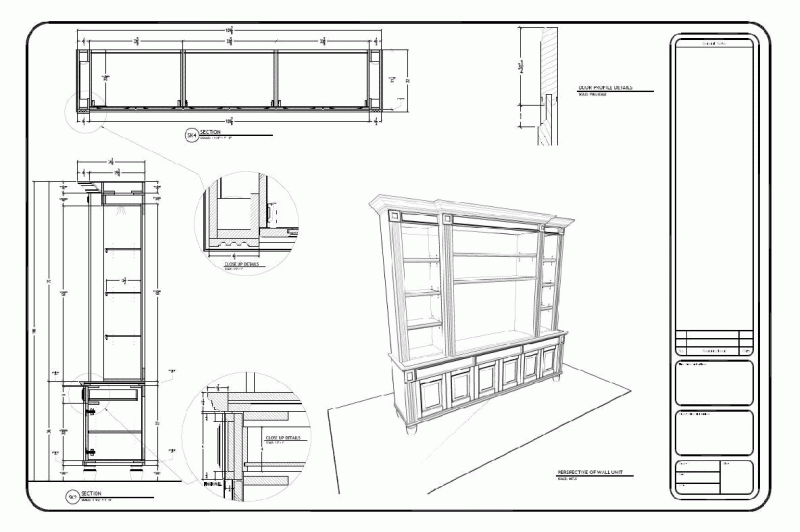
Click here for higher quality, full size image
From the original questioner:
Are those 100% MV? Great submittals...
From contributor I:
In my shop each draftsman does between $1.6 and $2 million/year worth of commercial work, a wide variety between casework and specialty products, almost all in Microvellum. This translates to between $800 and $1,000 per hour worth of work in my dollars, and if my math is right, about 10 labor hours worth of shop work is produced with each hour of drafting. The drafting includes most of the engineering needed for release to the shop, so roughly one drafter/engineer to feed 10 employees.
I don't know what good this kind of information does you, other than establishing a benchmark to see if you are getting better or worse. It would have been interesting to see how these numbers changed from pre-Microvellum to post-, but I never paid it much attention. There will be so much variation between shops due to pricing and product type that a cross shop comparison would be difficult.
From the original questioner:
Contributor T, I checked your website out. The shop I am at now does about the same type of work. We use Microvellum (sort of). Nobody here has more than a year's experience with MV and two of us (one being me) have never had the benefit of a training class. I am more of a CNC geek/3D modeling guy that started out working on a bench (self taught). Currently I program on laptop right next to the CNC (I prefer this to being in an office).
1K or 10 labor hours/drafting hour seems reasonable to me, using whatever tool (A-cad, MV or similar).
Initially generating the output was very simple. I used the architecturals to derive parts and modeled them and sent them to the router. It was much faster for me to do this than produce shop drawings and submittals, etc.
MV Question #1: If you draw a job in May for submittal and build in June or July, the tool diameters have changed and the material thicknesses have changed (white mel has ranged between .74-.765 and prelam sheets from .79-81). Is there a quick way to adjust for this? What we do is change tool file and the material file then redraw the products using the properties dialog box... cumbersome.
Question 2: How many of you use an AutoCAD viewer or similar to allow for non-drafters to review drawings without having to print? (None of our PMs know how to use AutoCAD.)
Question 3: Where and when do you print the labels/sheet layouts for the CNC? Currently we print them at the desktop and put them in a manila folder for the CNC operator. More time gobblers for the drafters.
Contributor Y, haven't tried that command yet... Teaching myself to make custom tools in Mastercam this weekend.
From contributor P:
For what it's worth, my numbers are 740 to 1600 per hour. My situation is a little different in that my drawings are amortized over many because we do multiples for retailers. I don't have automated drawings as with MV (just starting with Smartlister). The drawings do have quite a few revisions.
From contributor G:
One more question... This 1,000 per 1 hour figure, does that include the time to revise and put it to the floor? I had assumed it was just to put the drawings out for submittal. If it doesn't include that, how long is it taking anyone to revise the drawings after submitting and completing the package to the shop floor? I'm thinking we're about 50% of the drafting time for this step. That is, for every hour drafting, we spend a half hour revising and completing the package (CNC PGMs, sheet good optimization, revising and printing copies of drawings for floor, etc.).
From contributor Y:
The 1K=1H does not include the revisions on my part due to "you never know what the architect/designer/homeowner will think next." If the revisions are more than the normal "move this 1", make this cabinet 2" wider," then usually the companies I am associated with charge extra per hour whatever the revisions will take to complete. It is not the woodworker’s responsibility if the architect/homeowner changes their mind after the drawings are completed.
I have been working on a 250K game room. The homeowner changed his mind about 10 times on the design of the project. I have been working on and off for the last year on this project and the drafting hours went way out of control due to the homeowner. In this situation every time I have to change the drawings we invoice the homeowner whatever hours I put in. Sometimes it is good to hit them with these fees because they get carried away and they try to squeeze as much as they can from the woodworker. These revision fees bring the crazies back to reality.
Contributor R, those drawings were completed 100% with MV. Regarding the MV questions...
1. When you need to change the material thickness, just go to the job, change the material file and re-export the products to the spreadsheet. You do not need to redraw anything as long you have not changed anything crucial on the material pointers.
2. You can use DWF files for the shop people out back (as long as they know how to navigate on a computer screen). You can export the drawing on a DWF file by using the Publish command.
3. Regarding the labels. This can vary for every company. I usually recommend printing the labels on the CNC using Alis. Less time for the drafters and also it is better for the CNC operator in case something moves on the table and he needs to reroute a piece or two.
I recommend receiving a session or two of the MV's training. That will shed some light on a lot of the questions you might have.
From the original questioner:
Contributor G, I was looking at the submittal phase. As far as revisions go, I figure at least 50% of the original time after submittal. We spend about 10 minutes a sheet printing labels and sheet layouts when we use MV. With E-cabs I can put out about 30 hours of work/hour working off submittals or architecturals (all printing is handled at the router, material thickness is adjusted on the fly as you right CNC).
From contributor N:
I work as a freelance designer. In my country, most woodworkers/interior designers charge per m2. For a small company they rate from $10-$20 per m2. For a top designer they may charge $50 or more per m2. For custom made kitchen cabinet/big wardrobe, etc. we are using m'. We charge by length of furniture. We have a kind of standard for woodworking, such as D=60 cm and H=210cm. If more, they charge more.
From contributor C:
Does anyone know what percent of their gross sales goes to the cost of (engineering) complete submissions, field measuring, paperwork to shop, and project management?
From contributor E:
AutoCad keeps track of hours spent on each drawing. Look under File/Drawing Properties/Statistics. I suggest tracking your actual time and comparing to your estimates. Over time, you should be able to estimate closer and closer to the actual hours.
The comments below were added after this Forum discussion was archived as a Knowledge Base article (add your comment).
Comment from contributor F:
Relative to process, we have found that checking and reviewing are cheap compared to rework. Here is our flow chart:
1. Initial drawing based on whatever input we have (for us this is usually a manual drawing or rendering done by our designer).
2. Review by Project Manager and Designer and tecnical designer/draftsman to make sure it conforms with customer parameters and is buildable.
3. Review with customer.
4. CAD drawings (presently AutoCad) executed.
5. Review of CADs by Designer/PM/draftsman - at this time all notes on finish details, materials, appliance models, counter tops, etc are noted on drawings to be typed into CAD sheets.
6. Final CAD executed.
7. Quick review to make sure red lines are all done.
8. Email cads to customer/general contractor rof approval.
9. Draftsman does cut sheets for shop.
10. Qualified man from shop checks cut sheets for mistakes; questions on buildability may arise here.
11. Cut list updated.
12. Build.