Fabricating Stair Treads from Reclaimed Lumber
Woodworkers discuss ways to turn reclaimed sawn boards into stair treads for a house. February 6, 2010
Question
We are a cabinet shop working in a new home doing all the custom cabinetry. As such being the "woodworker" on this job, this question/work opportunity has come my way. The "new" floors being put down are 3/4" wide plank T&G reclaimed - old mill stuff - nail holes, cracks, and etc. supplied from the flooring contractor. He doesn’t know where it comes from. I am being asked to make stair treads from this material. There are 35 treads on an open type stairway, steel stringers with 1" x1" x3/16" angle iron welded in place, drilled for the treads to screw on. You see top, bottom and two edges. The builder says just glue up the pieces to make them 1 1/2" thick. I say no good. My thought is to re-saw the flooring to 1/4" thick and vacuum bag two sides onto 1" ply that has been edged with solid stock first. Code requirements?
Size of treads 11" X 36"
Find a mill to make and certify them?
Stave Core construction I don't do.
Guesstimate costs? $100 each plus material?
Opinions are welcomed.
Forum Responses
(Architectural Woodworking Forum)
From contributor R:
I don't think face gluing to increase thickness is such a bad idea. Custom door makers often do this. Of course face gluing wide planks is tough and perhaps you would be better off face gluing six inch rips and then edge gluing them to make the treads. Of course there will be clean up so you will never get 1 1/2" from two 3/4" pieces but do you need that thick? You didn't say what king of wood so I don't know if 1 3/8" would be ok.
As far as the idea of re-sawing them and gluing to ply I believe that anything over 1/16" thick is a sure failure. With the ends showing you would need to bread board the ends and that too will fail. Let us know how this shakes out! Guess a cost? First chose a method then apply knowledge of your own business.
From contributor D:
I'd just search around till you found some stock thick enough to get an inch out of. It would save you so much extra headache, depending on how much you have to pay (species). One hundred dollars initially sounds a little low for a "custom" application like this.
From contributor Z:
One hundred dollars each for material? That’s insane. Don't over think this. 36" span for 1 1/2" thick is fine. Just glue the stock for thickness. Forget all the extra wasted time with re-sawing and stave core etc. If this is an open rise stair then you still must meet the 4" maximum space requirement between treads. Solve this by adding a partial riser below the tread. This will also stiffen the tread. I'm all for making money but in my opinion this is pure greed. If the client agrees to pay you for work that is "make work" then I guess he deserves to get taken for a ride.
From contributor I:
Sorting, selecting, and then still running a nail through the carbide sucks! One hundred dollars tread plus material, amen! Otherwise, don't wait your effort unless you have nothing else to do.
From contributor S:
You didn't say how many steel stringers for this 36" stairway but I will guess two stringers. In my opinion an inch and a half thick board is not strong enough to span the full width and not flex with every step unless it had risers which would take away from the open concept. Even then I think flex could be an issue. I like the solid feel myself. I'd feel better with a 3rd stringer. Or a welder could weld heavy square tube from stringer to stringer that will also support the treads. This would take away the need for a middle support for treads.
From the original questioner:
These treads are between the steel stringers. There are two landings that will also be done in this material - heart pine 100 plus years old and dry. Glued down to the sub floor with Siko Elastermor adhesive and with all the large knot holes filled the stuff looks pretty good, but pickup a loose piece and you could snap it with the grain easily. The customer is adamant about maintaining the look and feel of the floors. There are no risers and steel reinforcement that shows from the bottom is not acceptable. The hand rail is S.S. with S.S. cables between the S.S. posts and Hitech with a rustic feel. Overkill in engineering and price is not the issue.
Flex is my concern and that is why I am thinking 1 3/8+laminated thickness. I have a lot of experience doing thick veneers vacuum bagged down. It's not like I have to worry about the material checking/cracking later. That’s the look.
From contributor D:
Reclaimed heart pine is out there in any size and dimension you can think of. If you want 4" stock or whatever you can get it. I'd go this route and forget the glue up option. It'll look better.1 1/2" may flex, 2" probably not. Somewhere in between might work too.
From contributor J:
Just remember to slot a couple of those holes in the angle iron for attaching the treads. Cracks may be fine, but treads broken in half-probably not.
From contributor A:
Like contributor Z I believe it's overkill. However, if you are going to use the recycled material as thick veneers, then you should be gluing it to the same wood or similar. Gluing thick veneers (3/8") to a piece of plywood is not a good idea. It will be weaker than using solid red oak as a "core", and really doesn't save much time.
Couple of questions:
1. Are the treads visible from behind?
2. Are the treads typ. bullnose?
I would edge glue a 3/4" x 2" strip of "old" wood between (2) 3/4" x 9" "new" treads with 3/4" x 1" strips at the edges of the clamps. That way you could use 24" clamps to glue up (2) at a time. Next, re-saw the veneers into approx 3/8" x 5 1/2" pieces. Likewise edge glue up (2) treads at a time. Then run them all through a wide belt at 60 grit then 100 grit. Throw them under the vacuum bag and then face/joint afterwards. Buy a garbage carbide round over bit from Grizzly and use it for this one job. Also, re-saw the "old" wood on the table saw not the bandsaw. Use some 10" thin kerf rip blade with 24 teeth.
From contributor D:
Hopefully the GC has already gotten approval for the open tread without the stiffener as contributor Z suggests. It ruins the open tread look IMO. I just finished an open tread stair that has 1.75" x 36" x 11" Brazilian cherry treads - very solid.
The connection of the treads to the stringers might be tricky with 1.5" stock since you cannot have any exposed steel from the underside. Simply mortising a tab into the tread will not leave a lot of wood above/below. If it was not for this, I would agree that you might be overthinking the problem. Then again, given the client, it seems prudent.
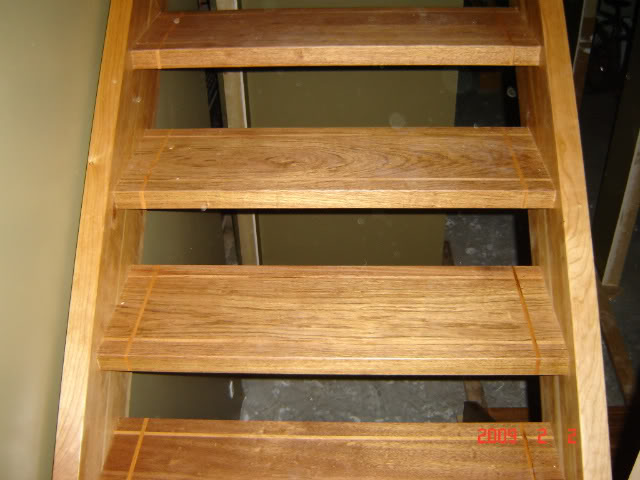
Click here for higher quality, full size image
"Photo by Brad Shipton".
From contributor S:
You have to charge first what it takes to make a profit and second what the job is worth to the client. IMHO, a buck a tread is a gift. I'd be charging at least twice that here in 'Planet California.' This seemingly simple job is a mine field in several areas. First, you mention this material is brittle. If it were me, I'd be using new material. It isn't hard to distress new wood to look like it's been around for a hundred years. It always makes me crazy to do it, but my first priority is to satisfy the client. I routinely make up samples for this purpose and get the finisher involved to make sure it's a true match.
Secondly, if it were me, I'd be using at least 1 3/4" thick solid material (No plywood core. If you try to glue this old material to plywood, you'll almost certainly have wood movement problems.) Even then there'll be some bounce.
Third, before you get too carried away, run a story pole for the stair rises. Mark the heights of the existing steel supports. Mark the thickness of the treads. Remember you only get 3/8" to play with.
I'll bet contributor Z's ancient band saw the steel is built and installed incorrectly. I've done probably fifty of these steel structure jobs over the years. I've yet to see steel installed correctly unless I've designed it myself and supervised its installation (which I do on a regular basis.) If, as I suspect, the steel is not right, I figure supervising it's modification into my bid or charge hourly for doing so. (A word of warning; this can turn into quite a food fight.) Check the plans to see what's spec'd for the stairs. That'll be what the steel guy hangs his hat on. You won't be popular with the steel guy for pointing out his boo boo.)
Fourth, my clients frequently want me to do something that doesn't comply with the code. Sometimes I'm willing to do so (exceed the 4" spacing on the treads) and sometimes I'm not (exceed the 3/8" max variation.) I take a risk in going along with the owner's request but when I do, I try to share the responsibility by drawing up what I call a caveat proposal. I say in writing what I think the code says, how the configuration requested by the owner may not comply (the 4" space maximum in this case) and that I'll be happy to modify the job (at extra cost) if the building inspector doesn't buy off on it. I show everyone (usually with a mock-up) how I'll do the modification if I have to. I get the client and GC to sign.
I don't pretend to be covered by this agreement but I sleep a little better. I'd close by saying this job is an example of why stair specialists are almost always busy.
From contributor R:
There is no way I would try to laminate that mess. The treads could be made easily from beams or decking like this company sells.
From contributor B:
He is asking for options on using the wood supplied by homeowner not supplies by others. I think your approach is the way to go. Old growth pine has very little lateral movement especially on such a narrow band when you consider you also have to edge with solids. The ply core will be very narrow. It is going to take 4-5 depending on rip width 4x8 sheets of ply+ machine time+ resaw time+ edge gluing+ face gluing+sizing+ nose machining+sanding+supplies+ delivery+profits. Sanding old growth is a real bear and time consuming. You know better what your hourly rate is and how long it takes to process in your shop set up. But I think $100 per each is low value.
From contributor R:
I was suggesting other old materials not that or any other specific company. The client doesn't always know best nor should we always bend to their ignorance to appease them.
The price he charges is his prerogative.
From contributor O:
Reclaimed pine is out there in abundance. Find a supplier that carries the stock in the thickness you need or thicker and dimension it. One important thing to remember is how the stair is laid out as to riser height. You have very little or no flexibility in changing the thickness of the treads without throwing your rise out of code. Also, having worked with the homeowner for this long I would hope that the homeowner might value your input and get the stock that you require rather than trying to make due with leftover flooring. For what it’s worth if the stock is so dry that you can snap it along the grain I would strongly consider getting a signed waiver holding you harmless when he goes through the treads and takes the short cut down.
From contributor W:
I think if you can get away with using solid at 1.75" or 1.875" thick it would be stout enough. Face gluing would be my second choice. It shouldn't be too tough to source some material that has plenty of thickness to it. Heart pine should have at the very least six growth per inch. If you can find some fine grained stuff with tight knots it should be plenty beefy enough. It seems strange to me that the wood they have is so fragile.
From contributor C:
I would do as you indicated in your original post but with a different technique. Don't attempt to face veneer that crumbly, knotty stuff in a vacuum bag. Instead, edge glue (if necessary) enough pine to get your width plus some first. Get a huge stack glued, planed and ripped oversize but identical.
Make a stack of pine, ply, pine, ply, pine , ply, pine, ply as tall as you think you can manage to face clamp together, and get through a band saw after they are glued up.Once you have a solid clump, then you can re-saw apart. Trying to make veneer first just won’t work because knots and chunks will be flying everywhere soon as you start getting thin with the planer. Even after they are re-sawed apart, it's a good idea to go very easy on the planing. The best way to plane that rust infested stuff is with a cheap four knife planer head running two carbide and two steel knives opposed in the head, even then you will be grinding often.