Making Raggle Boards
Suggestions on how to tool up for volume production of raggle sticks, and speculation about what a raggle stick is. March 9, 2010
Question
I have been producing raggle boards (the boards that have profiles cut into the sides for PVC pipe). I have been using a shaper, but wondered if there is a faster way - maybe a notcher?
Forum Responses
(Sawing and Drying Forum)
From Professor Gene Wengert, forum technical advisor:
I cannot figure out what you mean. Googled the term "raggle board" and it did not have any entries that helped. Can you explain further?
From contributor G:
Is this a raggle board?
From contributor S:
I would use a CNC.
From Professor Gene Wengert, forum technical advisor:
I agree. A CNC router would be ideal for this job. In fact, with today's slow economy, there are likely idle CNC machines that could do all you need for a very reasonable cost with a short production time too. Check both wood and metal processors in your area. Should you have a large contract, check for a used CNC machine.
From contributor C:
I would use a hole saw, then cut the piece in half to make a raggle board (whatever the heck that is).
From the original questioner:
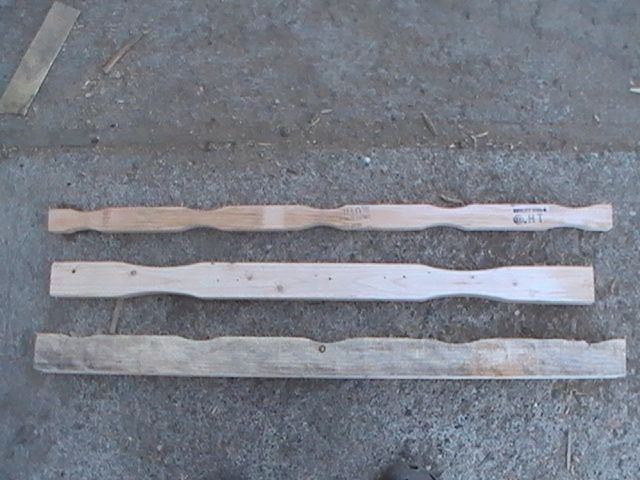
Click here for higher quality, full size image
Raggle sticks are made from 2x4s 2x2s or 4x4s and I make about 500 a day. Would a CNC be able to make that many?
From contributor M:
Yes.
From contributor A:
Baker makes a notcher for pallets and I bet they would make one that would spit them out pretty quick.
From contributor R:
I think more information is needed before suggesting the use of a CNC router for this job. In the first photo with the pipes in the crate, the pieces appear to be cut from plywood, and yes, I would agree that with a good vacuum table you should be able to quickly and accurately cut all your parts. However when producing the other parts pictured that are from 2 x 2, 2 x 4, and 4 x 4 stock, the problem is going to be holding the stock to the table. In order to cut 500 pieces a day, you need to produce a piece a minute. At that rate, you don't have time to jig individual pieces and hold them down with screws or other types of fasteners.
The machine I run is a Multicam MG series with a 7 hp spindle and a 20 hp vacuum pump to hold the material to the table. If I were producing the parts pictured I would start with the widest dimensional lumber I could get. Perhaps 2 x 12, nest the pieces inside the 12 inch width, line the boards up edge to edge, and do multiple copies of the toolpaths for as many 2 x 12s as you could get on your table, either 4 or 5.
The other issue I see is that cutting anything 4 inches thick on the CNC is going to be expensive getting tooling for. CNC machines are amazing tools, but they are not the best tool for every job and they are not cheap. Shop around with some of your pieces to a few shops and the operators will be able to tell you what their machines can do productively and what they can't.
From contributor C:
I would just make a jig to use a hole saw on a drill press. This should be fairly cheap to make (almost free if you use scrap lumber for the jig), and if made right, can have very repeatable results.
From Professor Gene Wengert, forum technical advisor:
My experience with a hole saw on a drill press is that with thick stock, it overheats and dulls very rapidly. How long would it take to cut a hole in a 4x4? Also, notice that the picture contributor G posted showing plywood holes is not very close to what the original questioner posted. They are not full or even half holes.
Using a CNC on 4" thick stock is an issue, but two half thickness cuts are made, one from each side (in other words, the piece is flipped over). CNC vacuum systems are very effective for holding work pieces. The cuts are made very fast, so time to make 500 a day is not an issue. Accuracy is great. In fact, several pieces can be put down at one time and the needed cuts made.
If you are close to NC State University, their extension forest products people may be able to help you run some test pieces.
From contributor A:
If you are making these from green lumber and low grade stock, then look at a notcher. They make them for pallet stringers and it would not be hard to adapt one to make the raggle boards. It would just be depth of cut and length. Baker may already make one. They make lots of crazy stuff for people. I have a shaper and it would cut the notches pretty quick with a jig. But if I had to cut 500 a day very many days a week I would look at a machine to make them. How are you cutting them now?
From contributor R:
I like contributor A's approach to this matter best. A dedicated machine for a specific operation. With all due respect for the doctor's opinion, I still don't feel the CNC is the best option for this job. However I would like to see the same photos and question posted to the CNC Forum to see how many CNC operators would be willing to take on the job.
From the original questioner:
I currently make them with a special jig and a spindle shaper. I think that a notcher is a good quick way to do it, the only problem being I have 10 different radiuses and the quote I got for notcher blades was 3000 per blade. Still, would a double head notcher notch a skinny board 1.5 x 1.5 x 42?
From contributor Q:
Have you considered just a good old heavy duty bandsaw? You can use a pattern and guide much like you would a shaper and probably a lot faster. I would venture to guess these are not real super tight tolerances, but I may be wrong. As owner of a CNC router, I would not be excited about running these parts just for the wear and tear on the spindle for what I assume is a low margin product in pretty tough material.
From contributor Z:
Contact Ken Gore at Baker Products and I bet we can get the cutter to make your desired notch to fit our Bantam or Auto Single notcher. All we would need is the depth and spacing of the cut you need.