Shaper Fence for Raised Panels
A cleverly made auxiliary fence for the shaper makes it easier to accurately machine raised panels for cabinet doors. February 29, 2012
Question
I am in a real need to upgrade my approach to panel raising. I am currently using a Kreg miter gauge and a Delta 3hp shaper to do my raised panels. It works but is not the safest and doesn't yield the greatest results. I have been thinking I would purchase a low end sliding table shaper (5hp). How do you do it? Is the sliding table the best approach to getting safe and consistent results? I already have designated shapers for the other operations, so I didn't think a Unique or other just door machine would be the best use of money, but I am open to input.
Forum Responses
(Solid Wood Machining Forum)
From contributor R:
There is no need to use a guide or slider to raise panels. Run the panels face up with a feather board or feeder. A power feeder is best for safety and quality of cut. With the cutter head above, this locks in the critical thickness at the edge so it will fit precisely in the groove of your frame. You can make an auxiliary fence with a continuous hardwood strip on edge underneath. This will give full support and added safety to the panel regardless of width as it traverses the tool opening. Save the sliding table for your rails.
Martin USA, by the way, has an affordable slider that will bolt on any shaper and is easily removed when you do not need it.
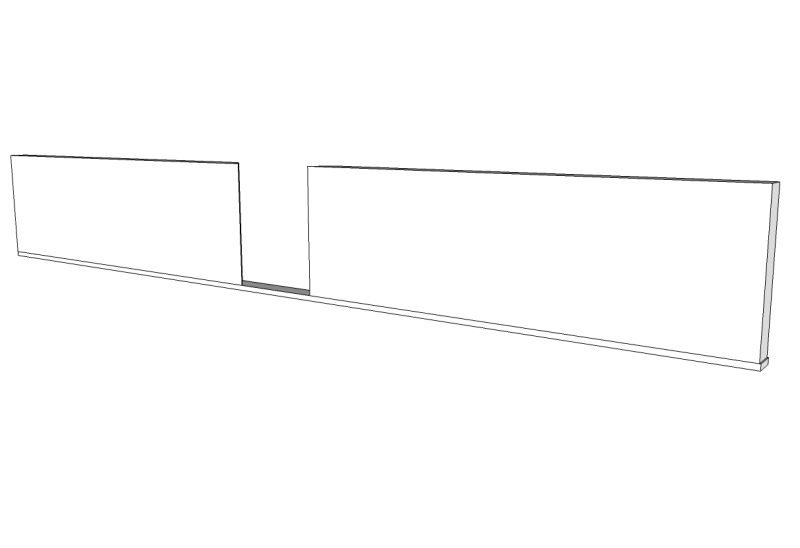
Click here for higher quality, full size image
From the original questioner:
Thanks. I don't understand how you use a feeder with raised panels. Many of the panels are only 5" wide. How do you safely run a 5" wide panel though a 6" diameter cutter? That is where I was using the miter gauge to guide the panel through the cut and not kick back. I do have a Steff 2034 feeder on that shaper, but I haven't tried to use it for panels because so many of them are small and narrow. Am I missing something?
From contributor R:
The key is the strip (aluminum works well also) below. There is no way the panel can dip into the cutter as it is fully supported over the entire tool opening. As you engage the feeder you will also want to help it along by keeping it square against the fence. You can't simply let it go as you would a long edge. You can also double up in width for your very narrow panels if you wish, as the end grain needs to run first anyway, then rip and run the long edges.
From the original questioner:
That makes great sense. I will try that setup. I have a one piece fence on it now, but the bottom is not continuous. So if a new tool is in the mix, would you get just a regular 5 hp shaper 1.25" spindle? I need to upgrade that shaper, because I feel it lacks sufficient power for panel raising, and it only has a 3/4" spindle. I would like to go to 1.25" insert tooling, so an upgrade is necessary. What would you buy?
From contributor R:
If you want a heavy shaper I would recommend you buy used. The SCMI T110 is a good choice and there are quite a few listed on this site.
From the original questioner:
I set up my current shaper just as you described with some aluminum flat stock and my feeder, and it worked excellent! I can hold off on that shaper purchase a little longer now and save for a nice euro machine. Thanks again for the help!