Shopping for a CNC for the Small Shop
CNC for the small shop has come a long way in recent years, as this conversation demonstrates. There are many excellent options on the market, and many factors to consider. January 3, 2012
Question
I have a two man shop and I am in the market for a CNC. I initially looked at the Shopbot PRS Alpha. I have eCabs, so I liked the idea of saving money on the software side of things. But I can't get over the table with its aluminum and bolts. I like heavy.
So I have narrowed it down to the Camaster Cobra or the FMT Patriot. They look comparable on paper. The Patriot is all ball screws, however. Then again I am cutting pre-finished plywood, not space shuttle parts. The Camaster Cobra has a three head version (poor man's tool changer), so I am thinking of a 5mm bit, a 3/8 bit, and something else. I would have to add an air drill to the FMT. Camaster have been around longer than FMT. They are both American companies, so from that standpoint any decision is a good one. My concern is support and maintenance. I like the idea of a turnkey machine.
Forum Responses
(CNC Forum)
From contributor M:
Have you looked at the less expensive line that Thermwood has been building? You absolutely can not beat their service/support. And since you are already using eCabs, you will be saving a huge amount of money and learning curve right there. That has to be worth 20k. Everything in your post leads to a Thermwood (and no, I am not a salesman for them, but I do own one).
From the original questioner:
Thanks. Didn't know they had smaller machines. I am thinking of migrating to KCD though. Which models are smaller, the 43? Do you know what range they are in?
From contributor K:
Contributor M is correct. Do yourself a favor and look into the Thermwood CS-43. It is a great industrial quality machine and you already have the software to run. One of the best things about Thermwood is that they do it all - they build the machine, the control and have written the design software to run the machine, so for service you just need one contact. If you want American made, Thermwood is the oldest name in the business.
Why would you want to change to KCD when you already have one of the most powerful software design and manufacturing packages available?
From the original questioner:
Because I can't afford a Thermwood and I don't want a Shopbot.
From contributor I:
When looking at the installed price of the machines in question, not including software, I do not believe these would all fall into the same price range.
From contributor S:
You could always get the control box from Shopbot and use it on the Cobra or Fmt. That way you could still use the Ecabinets software. I've heard other people have done something similar.
From contributor H:
I spent 2 days at the Thermwood factory last fall. I already owned a Holzher router (heavy metal) and it is a splendid machine. Looking at my purchase of the Themwood, I get great service, parts in America at reasonable prices, software that is made for the machine included, upgrades included, ability to run CAD DXF files, etc. It's a great machine for nesting, especially since I didn't have to invest in new software which would mean costly upgrades down the road. They answered all my questions, supplied me with training at the factory for a week, and if I wanted, I could have purchased online tech support right at the machine, which I'm sure other companies also offer.
Friend of mine purchased another brand 6 months before my purchase - good heavy metal machine, but no quick cut option, no profile modeler, and he purchased additional software for his router at over $20,000 to get what he wanted. He's happy... good machine, over 100k purchase. Thermwood router, software and all, not anywhere close to that amount. My router also uses 1/4" spoilboards as waste boards so I'm not going through 3/4" material as the other router does.
From contributor K:
I think you have to include the software in the price while shopping for a machine. The software is just as important as the machine and can add $10,000 to $20,000 to the cost.
You probably need to look first at what you want the machine to do for you and look to the future. I would think a tool changer is a must have. An inexpensive machine that won't do everything you want it to do is no bargain. The same goes for your software.
From contributor E:
I have owned and operated a Camaster for 4 1/2 years. I am very happy with my machine. It has done everything we have needed in my 3 man shop and we have not even scratched the surface of what it can do. I looked at Shopbot before I bought the Camaster and I agree with you about the aluminum and bolts. Just not what I was looking for. You absolutely will not go wrong with Camaster. Customer service is an understatement! They're always willing to help. They are dealers for KCD. I use Cabinet Pro, Cabinet Vision and V-Carve.
From contributor J:
In the fall of '07 I decided to go CNC after years of swearing I would never own one. The CNC salesman had traditionally only spoken voodoo and promised the moon to get my business. After all the internet searching and a visit to the blue bolt together factory in NC, I called Camaster and asked if there was one close to me that I could see. They referred me to someone in Camden, SC a few miles from me. At that point the machine was still a hunk of iron with a spindle on it, yet I was enthused by the relationship he had with the owners. This is what I had to have as I knew nothing of code, programming, and all the new learning curves that come with CNC. What I saw that day let me know this was something I could no longer live without and I would need a patient teacher.
I have now owned three Cobras and have one Stinger. I purchased one of the first X3 machines built (#5) and it performs as well now as the day it got delivered. I got involved with the support forum, which is machine owner moderated and eliminates any of the old voodoo rigmarole from the closed cell CNC world. The machines are universal and open architecture in mechanics and software. There is not a part on it I cannot get from several sources and replace myself in a short time. I have never been down more than an overnight shipping day, and keep a few parts to prevent that. The support forum has over 700 teachers most hours of the day, and with the direct screen to screen training (free), all costs are contained. The forum has drawn the support of several software companies and will support their products used by Camaster owners. It is still almost unreal how valuable that is!
Last weekend I hosted an Aspire Camp for owners of the Vectric software. CAMaster had a training session with a good many owners. The photographs of the camp and the work shown are from owners of the software, which includes CAMaster owners. This work was also done on Shopbots and other machines and I would be wrong not to give them credit. The way I see it, CAMaster may not be the biggest CNC company, nor the best, but it certainly is not second best to any in its class.
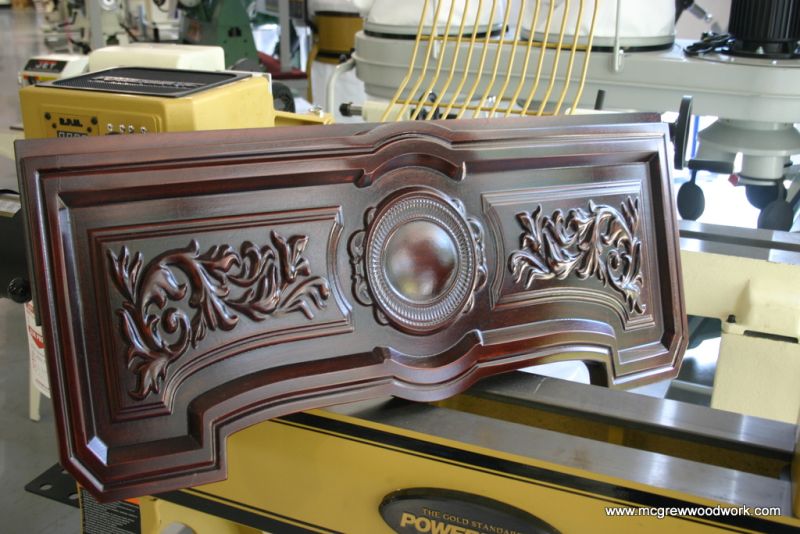
Click here for higher quality, full size image
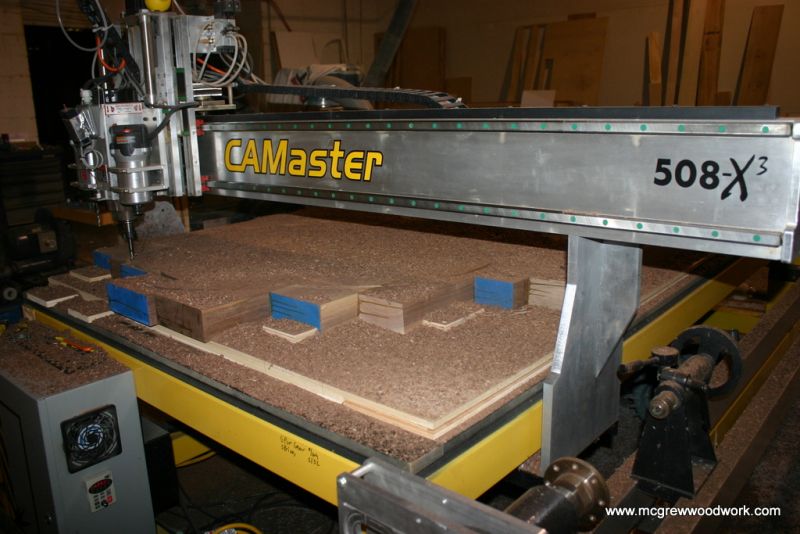
Click here for higher quality, full size image
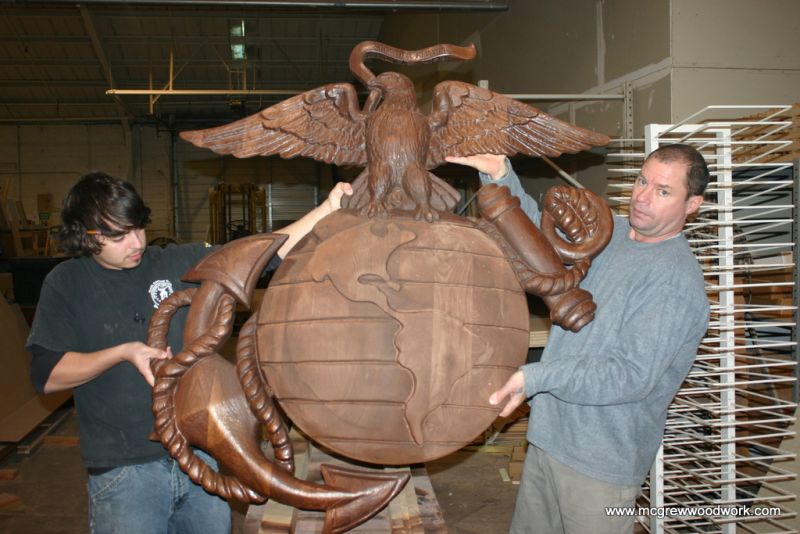
Click here for higher quality, full size image
From contributor K:
Nice carving work as always. What software are you using to design, nest and manufacture cabinets? Are you happy with it? Is it powerful enough to design everything you want to build? What cost did it add to your machine?
From contributor J:
While I have eCabs, KCD, and Cabinetpro, I use Cabnetware to design most all casework. I design and nest custom parts with Aspire (dxf batch import, nest, toolpath templates setup) and casework parts with Cabinetparts Pro. I purchased Cabnetware in 96 and upgraded in 09. The difference in screen to machine and my method is about 6-10 minutes of entering sizes in Cabinetparts Pro. Most times now I ask the architect for the CAD drawing and simply import the DXF and machine with Aspire from there.
As far as cost, KCD and Cabinetpro will draw and nest to CNC. One can get more powerful software. What I really think we need is a 2d floor plan, face elevation and cut profile software in black and white (no 3d) which will nest to CNC or export a DXF to Cabinetparts Pro (250.00) or Aspire/vcp (600-2000). You can spend a lot more. I just don't and have not found it necessary. eCabs has potential yet it also will not produce a cut profile for shop drawings. Our mutual friend in Michigan loves it. Recently we found the small program Cabinetplanner will produce nested DXFs for euro and face frame cabinetry and export to Aspire or Cabinetpartspro. It cost only 90.00 and is an amazing program for the money.
One can spend some big bucks quick and actually slow down the learning curve in doing so. I always suggest get a good machine, learn the basics, then decide on software. Buying software at a machine purchase can be an irreversible mistake if it does not suit your needs.
From contributor K:
I am glad I don't have to draw in Cabnetware, Cabinet Parts Pro and Aspire to nest a job. I would never get it done. Draw in eCabinets, click the CNC button, and I am done. What is a "cut profile" for shop drawings?
From contributor M:
I will second what contributor K said. I have seen several packages up close and used some of them firsthand. I have seen what it takes to get a cabinet out of your library and put a hole in a side or something.
It's crazy some of the hoops you have to jump through for the simplest things. In eCabs, you pull up your cabinet in cabinet editor, take the part in to the part editor, do whatever to it, hit the CNC button and your file is written. If your router is on your network, the file is waiting at the router for you.
And the best thing is that if there is a problem, it's the same phone number and no one there will pass the buck to the machine guy, the post guy, the software guy, etc. I am sure there are many good software packages out there and some of you do killer work, but I would never consider another machine or company.
Contributor J, your carvings are awesome. I have Art-cam and wish I had personal time and machine time to do some of that type of work.
From contributor J:
Thanks. I have had to incorporate it (the carving) into work for money. I would love to tell you I am some kind of independent wealthy artist, but the answer to that is definitely not!
Contributor K, I have always been under the impression you are a designer (eCabs and well respected for it too!). Do you actually have a CNC machine?
From contributor K:
I have what I call "Outsourcing with Benefits." Contributor H that posted above recently purchased a Thermwood 43 and I am outsourcing my box parts from his shop. I went to the machine training class with him and his shop foreman and he is letting me cut my own parts on his router, which is giving me some great experience. I have been really surprised how easy the machine is to operate. I am now getting the full benefit of eCabinets.
From contributor M:
Would it not be great to just be able to turn paying customers away and have the shops we have to play in? I would still come to work every day, but just lock the doors and turn off the phone... Maybe produce something occasionally for just the right customer!
From contributor B:
"The Camaster Cobra has a three head version (poor man's tool changer), so I am thinking of a 5mm bit, a 3/8 bit and something else."
Be aware that multiple head machines usually mean a reduction in functional table size. If a dual head machine has 2 side by side spindles 8" apart, your table width is functionally reduced by 8".
From contributor J:
The CAMaster X3 has a gantry that is supported on the vertical gantry plates and is extended in each direction beyond the table to the necessary offsets required. All spindle and routers (or all spindles) reach the full potential of cutting area on the table. There is no loss. I had an extra three inches of overhang and moved my gantry over to one side of the table and added a 12" diameter rotational lathe on the side of mine. This move will let two of my spindles work over the lathe. This configuration of gantry allows for tool changer setups to be placed on any end or side of the machine as well. Every once in a while, I decide to carve a 4-6" thick piece so I just exchange my gantry risers for a taller set when I need it, then lower it for most work.
From contributor P:
Just FYI, CAMaster is assembled in the USA but the linear rails and bearings on the Cobra are Chinese. As above, you'd be better off with the entry level Thermwood.
From contributor J:
Sorry to have to correct an uninformed response, but the bearings and slides on the Camasters are Hiwins.
From contributor F:
Hiwin is Chinese.
From contributor R:
The comparisons I see between the FMT and CAMmaster are... CAMmaster has aluminum risers and bridge tube versus FMT all steel construction. CAMmaster rack and pinion versus ballscrews FMT. CAMmaster PC based controller versus industrial style Fagor on FMT. If the prices are close to the same, FMT looks like better value.
From contributor J:
There isn't a machine mentioned in this thread I do not think well of and recognize the individual value of. I am grateful the market has changed and at this level we have excellent choices. Three to five years ago this was all large iron, big money and voodoo to a small shop. Smaller CNC companies took root, created a great product, and forced larger companies to compete.
From the original questioner:
I was born and raised in Ireland as a result I will only buy American or Irish.
From contributor T:
I understand your Buy American ideal. But in the CNC router world, it’s a relative term. It’s fair to say that that machines you mention (including my company's, NEW CNC) are assembled in the US. We all use component suppliers for spindles, linear guides, ball screws, rack and pinions, bearings, air cylinders, electrical parts, wire, push buttons, computers, even nuts and bolts. I cannot presume to speak for the other companies; here at NEW CNC we spend the largest amount of assembly time on the wiring, the CNC control box, and software. We do about 2 weeks of assembly to each machine and then testing before the name goes on.
All of the design work is done in Michigan and as we develop we continue to carefully examine whether to buy or build each and every part of the machine. What each company spends their time doing is a matter of management direction and vision for the company. We engineer, wire, build controls, finish assemble the bridge and base and develop CNC systems. We do not weld. We think that the relative value added for welding is low, so it’s outsourced. Other companies weld the frame but buy the CNC control. Again it’s a matter of management direction. I’ve attached an example of the construction of the bridge. It shows the internal bracing we use. It’s not common to have this kind of construction on a machine in our price category.
Ask any of the companies you are considering which parts are US made. Many of the parts we purchase locally in Michigan are actually made overseas. It’s the global economy we live in. The NEW CNC machine is assembled in Michigan. We actively decide which components we buy and which we build. Every machine builder makes choices on buy or build. We think that the mix we use has tangible benefits for the machine owner.
If you stop to look at the actual machine tool on your shop floor, consider that you are, or may be soon, using that machine to compete with every other company on the planet that has access to your customer. It’s a good bet that your customers will be exposed to more and more of your competitors as time passes. You will be competing on a global scale sooner rather than later.
From contributor R:
Where do the spindle, ways and bearings and the rack and pinion come from? Japanese cars are also assembled in the US. However they are still Japanese cars.
From contributor M:
Once again, Thermwood - take a plant tour.
From contributor I:
Thermwood is a fine product, and please correct me if I am wrong, but the machine you are suggesting is twice as expensive as the other three mentioned in this thread.
From contributor T:
Our spindle is made to our spec at a large plant is China. We use Hiwin rails which are made in Taiwan. Our local rail supplier is in suburban Chicago. The bearings are Japanese NSK. They are in Ann Arbor, MI. Our rack and pinion manufacturer is in Germany, Atlanta Antriebssysteme. The local supplier is in New Jersey. It's not a secret that all of the made in America machines outsource their spindle, bearings, rails, rack and pinions, and/or lead screws too.
From contributor C:
Whatever you do, get it all in writing - if it's not there, you have no recourse. I have been working without a tool changer for 6 years. Whatever you want, get it in writing.
From the original questioner:
FMT is owned by DMS, a big iron American company.
From contributor N:
I run a Shopbot with aluminum rails. I had to do some beefing up on the frame, as it was too shaky. Running the ecabs files with it is nice, but I don't think I would buy another Shopbot. I would be putting a Shopbot control system on a Cammaster. Then you get a better machine and run the software you know. If you could find a gently used Thermwood, that would be nice though. All in all, my Bot has paid for itself and the resale value on them is great. Used ones get sold very quickly, so upgrading won't be a problem. My only complaint is that I waited so long to jump in.
From the original questioner:
I have a demo of KCD and it looks way easier than eCabs. On the other hand I have been thinking of going the AutoCad and Smartlister route. I am tired of workarounds. I am pretty decent with AutoCad LT.
From contributor C:
No matter what you buy CNC wise, the payback is very fast, and although I have had some issues with my first purchase, my CNC has paid for itself easily by the first quarter of each year.
From contributor K:
KCD may seem easier, but what are you going to do with it? Try building the speaker cabinet below with it. You can do it with AutoCad and Smartlister but you will be working one part at a time. A large kitchen that way will be no fun.
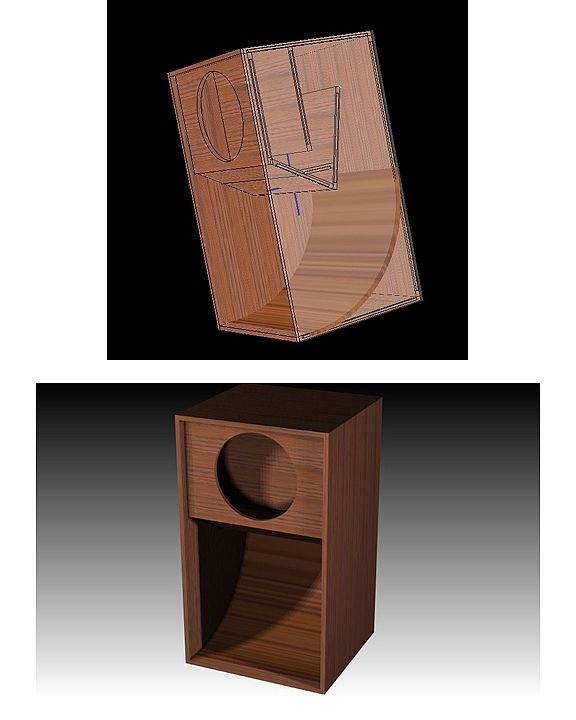
Click here for higher quality, full size image
From contributor R:
If you are making a purchase with an eye on resale value, a large part of that resale value is perceived quality and longevity over time (Honda, Toyota). Mechanical items sourced from China have not gained that level of acceptance yet, resulting in decreased resale value.
There are plenty of unemployed welders in Michigan too. Add value to US manufacturers by utilizing American labor.
From contributor U:
I'm extremely pleased with my FMT Patriot. Software, on the other hand, is a much tougher decision and I'm not certain I made the right one.
From contributor O:
I have owned and used CNCs for over 18 years, and now sell them. The first thing you should do is thoroughly check out the company. Pull a D&B on them. Why? There is at least one company mentioned in this thread whose owner has gone bankrupt at least twice - closed down, moved and started up again under a new name. You should have confidence that the company you buy from is going to be there to support you years from now. Make sure that the company you buy from has a long history of good financial health. You would not extend credit to someone with a 600 credit score, so why would you buy from a company that has a 65 BD rating? The last thing you want is to invest $40k in a machine and then find that the company leaves you holding the bag when you have problems.
Next, consider the company’s ability to train, help, and support you after your machine is installed. I know too many folks who have machines that are basically collecting dust because they never received the help and training they needed after the sale. I started my company for just this reason. Many local salesmen don’t even know how to turn the machine on, let alone help you with a machining, tooling, or programming challenge. It is critical that you buy from someone who can and will help you through the learning curve and be there as you grow. I have customers who purchased machines 3 years ago that I still go help with advanced applications and machining techniques.
Don’t get a machine without a tool changer. The little extra that an ATC costs is well worth it in the end. Don’t get a machine that is predominantly aluminum. Vibration is your enemy and aluminum does not absorb vibration like steel does. Don’t get a machine that’s built on a bolt together base for the same reason. There is no rigidity and they vibrate. Cut quality, speed, tool life, and overall machine life will suffer.
If you are worried about resale value, you need to look at the big names. These small machines will get the job done and pay for themselves over and over again, but you won’t have much resale value left in them when they are 4 or 5 years old.
Don’t skimp on software. I know free software sounds great but it’s free for a reason. They want to lock you into buying their machine and free software is the hook that they use.
Be wary of the machines that come unassembled and you assemble yourself. On the surface it may seem that you are saving money but you are buying a machine to work, not one to work on. It should come to you ready to run right off the truck and you should get professional onsite setup and training with it.
Be wary of anything proprietary or closed architecture. The machines I sell run on industry standard g-code. Machines that run on proprietary controls will limit your flexibility and likely cost you more to own in the long run.
Lastly, take the specific brand advice on this board with a grain of salt. Most machines are good machines. Machine owners tend to be loyal if their experience has been relatively good. Most, however, do not have broad experience with multiple brands. The bottom line is that a CNC router should be the best investment that a person can make in their company. If done right, the machine will have an immediate positive impact. If done wrong it will likely sink you.
From contributor Q:
Also look into power requirements. A friend of mine got a cs45 Thermwood. Been sitting for a year. The electric company says he can have 480v 3 phase for another $80,000. I have tried to do a phase converter, but it can't energize the step-up transformer. If I could afford it I would buy it from him, but 87,500 is a lot if you don't have enough work for it. The catch is you have to have it before you can do the work, unless you start outsourcing first.